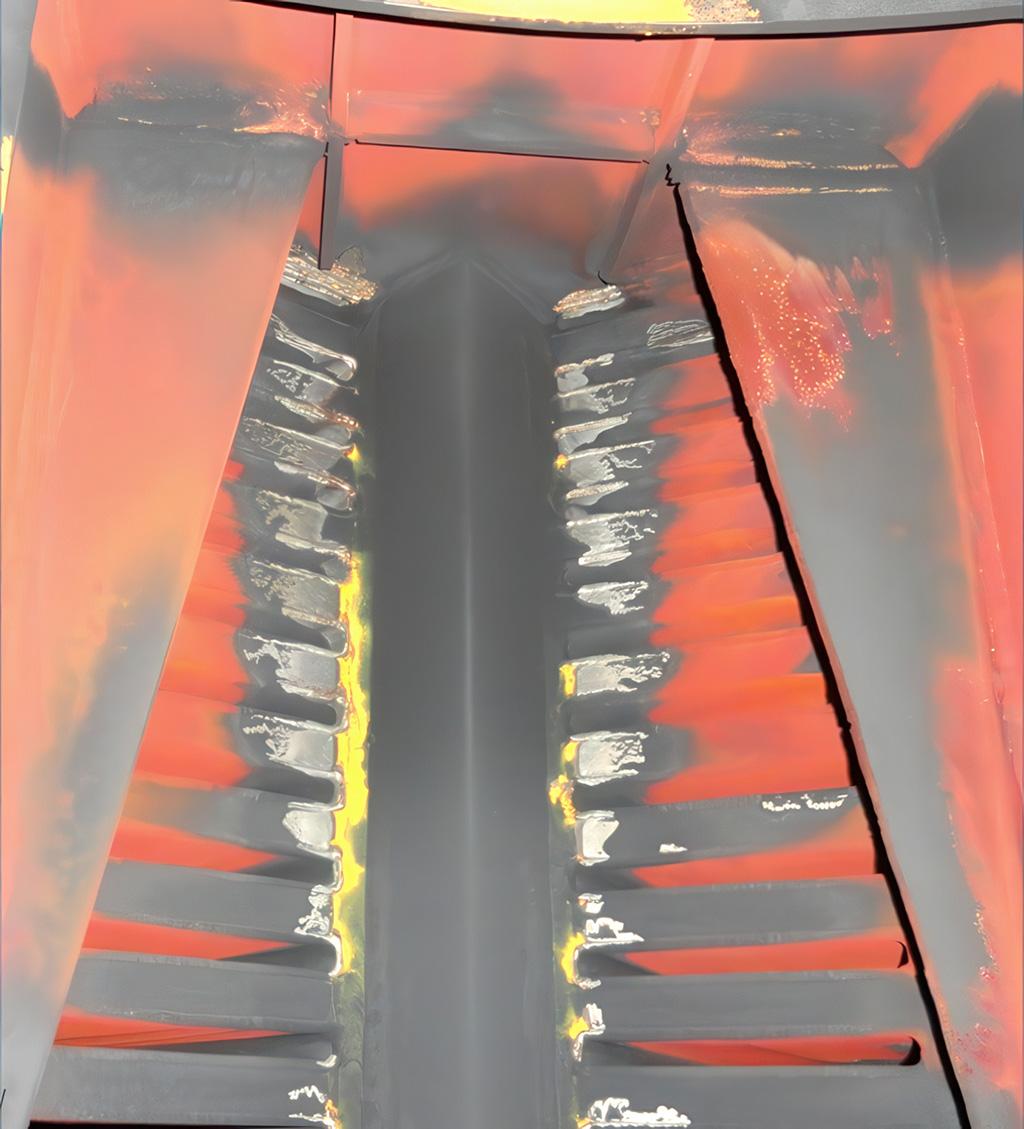
Corrosion at steam entries to ACC HX finned tubes
Project Highlights
- Identify a host site where the full-scale project can be executed
- Develop a test plan to carry out the project with input from participants
- Perform ACC inspections prior to chemical feed, and at project conclusion
- Evaluate data, report results, observations, and conclusions
- Improve understanding of the potential benefits of managing corrosion in the ACC with feed of ethanolamine to the LP turbine exhaust
Background, Objectives, and New Learnings
Air-cooled condensers (ACC) are increasingly being employed in thermal power plants, as access to water supplies and regulatory requirements for water discharge have become progressively more challenging. However, cooling by ambient air requires a much larger surface area than cooling with water. ACCs are therefore designed as very large carbon steel structures to accommodate the required heat rejection.
Due to their large internal surface area, ACCs can experience the formation and transport of a larger quantity of iron oxide corrosion products compared to water-cooled condensers under the same cycle chemistry conditions. In addition, the thin-walled heat exchanger tubing can be susceptible to through-wall penetrations due to local steam flow and chemistry factors.
Elevating pH to >9.8 with ammonium hydroxide is a proven method of reducing the dissolution and transport of iron from the carbon steel surfaces. However, the high volatility of ammonia limits its capability to increase pH sufficiently in the initial condensate of the turbine steam exhaust. As a result, many ACC operators have found that steam-side carbon steel corrosion is not adequately controlled using ammonium hydroxide alone. In some cases, a neutralizing amine with lower volatility and slightly higher base strength has been added to the steam cycle with the intent of increasing the pH of initially formed condensate. However, neutralizing amines are subject to partial thermal decomposition in high-temperature steam superheater prior to reaching the LP turbine and subsequently the ACC, requiring more amine to achieve the desired outcome. Furthermore, the decomposition products generated by the amine are weak acids and may lower the pH in the condensate, as well as contribute to cation conductivity measurements and mask the presence of highly corrosive contaminants such as chloride and sulfate.
Direct ethanolamine (ETA) injection into steam turbine exhaust could overcome this limitation. This project seeks to conduct a full-scale trial to determine requirements and effectiveness, including chemical injection and pH control, decomposition byproduct accumulation and impacts, and evidence of ACC steam-side corrosion reduction.
Benefits
Targeting the feed of a neutralizing amine directly to the area of corrosion concern may result in more effective pH control and reduction in corrosion and subsequent iron transport. Reduction of ACC steam-side corrosion minimizes risk of long-term reliability losses and performance loss from air in-leakage. Carbon steel corrosion in the surface area-intensive ACC may cause excessive levels of iron oxide transport to the steam generator, resulting in higher risk of tube failures.
Testing this novel approach to ETA injection downstream of the high-temperature superheater may provide ACC operators with another option for managing ACC corrosion.
Project Approach and Summary
The project involves a full-scale test involving the injection of ETA into the turbine exhaust before the ACC at a host site. The ACC will be inspected prior to, and following, the test period in order to observe and evaluate the direct effect on carbon steel corrosion. Steam cycle monitoring will be conducted for relevant parameters: ETA and its breakdown products acetate and formate, along with chloride, sulfate, sodium, pH, oxygen, specific conductivity, degassed cation conductivity, and iron. The data will inform ETA feed rate adjustments during the test period. At the conclusion of the test period, a technical report will describe the test results, learnings, and conclusions toward applying the technology to generating units equipped with ACCs.
Deliverables
The deliverable for this project will be a report describing the results and their potential application to plants with ACCs.
Price of Project
The cost for participation in the project is $60,000. Host pricing will be determined based on the specifics of the project. This project qualifies for self-directed funds.
Project Status and Schedule
The project was initiated in fall 2024, with a pre-exposure inspection of the host utility ACC steam-side. It is anticipated that the ETA injection and monitoring test period will require 12 to 18 months to provide adequate data, and the project will conclude with a post-exposure inspection of the ACC. The conclusion date is estimated as no later than fall 2026.
Who Should Join
This project is applicable to owners and operators of thermal power plants, including combined-cycle plants, equipped with an ACC.
Contact Information
For more information, contact the EPRI Customer Assistance Center at 800.313.3774 (askepri@epri.com).
Technical Contacts
Brad Burns at 704.595.2437, bburns@epri.com
Andrew Howell at 980.215.1805, ahowell@epri.com