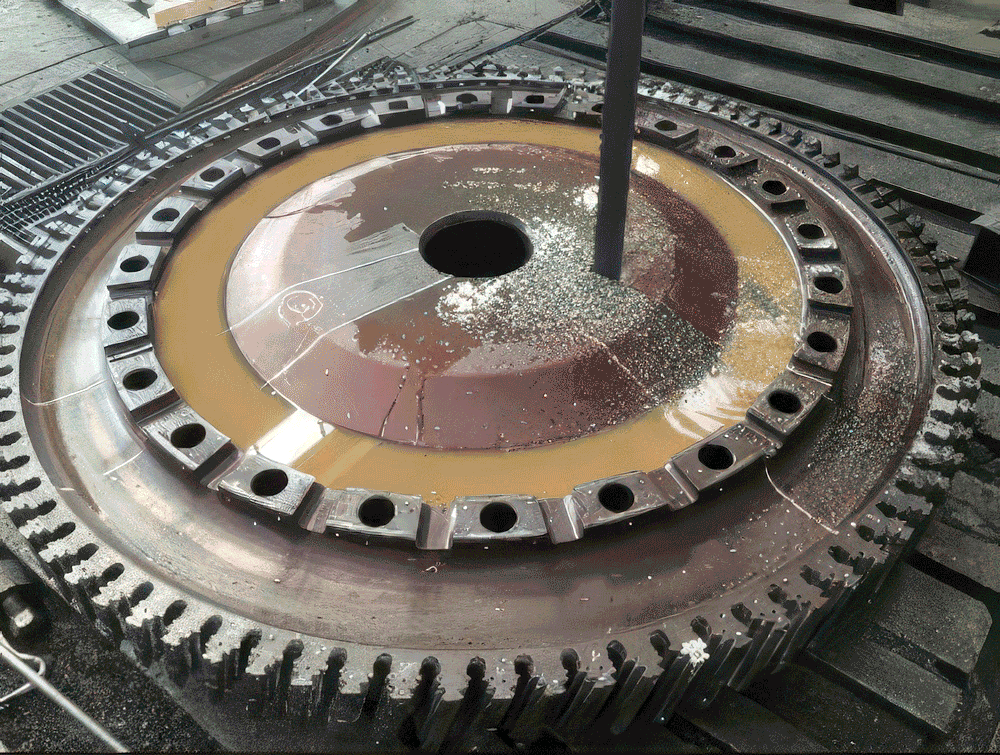
Utilizing IN706 Material Data to Assess and Lower Operational Risk
Project Highlights
- Establish clear and technically informed strategies for rotor life extension and associated risk profile
- Develop relevant material property data in service exposed IN706
- Enable life extension for gas turbine rotors in hours- and/or starts-based operational profiles
Background, Objectives, and New Learnings
Natural gas combined-cycle units are playing a prominent role in the energy transition, and many units are reaching original equipment manufacturer (OEM)-design life cycles for major components. The earliest installed F-class units now have >30 years of operating history and many more units are approaching the OEM end-of-life cycle (e.g., 144,000 hours or 5,000 starts). The GE 7F model accounts for 950+ globally installed units producing >175 GWs. This frame model will be a key focus for this supplemental project. Assessment of newer models (e.g., 9H) that utilize IN706 material will also be considered for this project, including generation of the appropriate material property data. With large industrial gas turbines expected to play a critical role in efforts to achieve net-zero, comprehensive life management strategies are needed for aging fleets. The most critical and expensive component (the rotor) will be the focus of this supplemental project. The development of informed data to support life extension for the GE 6F, 7F, and 9F rotors will be the primary focus, including relevant destructive tests in widely specified materials, such as IN706. This material is used for major components, for instance the first stage wheel and spacer. Funders will have the option for leverage the project outcomes to inform a fleet-wide or individual rotor life assessment (as a billable service agreement).
Benefits
This project is expected to help participants implement an integrated strategy underpinned by comprehensive materials data to extend the operating life of rotors installed in F-class industrial gas turbines. All funders will obtain the generated data supporting the life extension of rotors utilizing IN706 material. The findings from this project will help address a key industry need for improving the reliability and safety of aging gas turbine assets.
Project Approach and Summary
Task 1 – Operational Analysis. Funders will gain insights into understanding how operational profile (such as firing temperature, starts/starts, hours, etc.) influences potential risk associated with lifetime extension. This will include consideration of the current the current OEM-specified design life of 144,000 hours or 5,000 starts.
- The project will evaluate several different units that span a wide range of operational and design profiles, such as:
- Predominantly baseloaded units (hours-based)
- Gas turbines that experience numerous cycles and operated as peaker units (starts-based)
- Influence of upgrade packages and design differences (e.g., 7F.03 vs. 7F.04 vs. 7F.05) and the impact these have on past or future life consumption
Task 2 – Mechanical Testing and Characterization. Developing high-quality and relevant mechanical testing data and detailed microstructural characterization in ex-service rotor material will serve as a critical criterion for supporting life-extension plans. EPRI has access to the material of interest, and will seek additional ex-service components to support a wider set of informative destructive tests. Previous testing in IN706 material will be leveraged for this project. To inform this task, the project is expected to perform the following tests:
- Mechanical test data in IN706 material under various conditions and examining variables, such as heat treatment, service exposure and long-term aging
- Development of test methods to generate relevant data that evaluates the susceptibility of IN706 to Stress Assisted Grain Boundary Oxidation (SAGBO)
- Test data to support hours-based vs. start-based approaches for life extension (e.g., fatigue with hold time, stress relaxation, and other data)
- Characterization and damage assessment of service-exposed rotors
- Detailed post-test evaluations following completion of destructive test programs to link key microstructural features in the pre-test condition to the observed post-test damage condition
Task 3 – Risk Assessment Tools. Evaluation of mechanical test data and the assessment of available operating profile will be leveraged to develop risk assessment tools to inform life extension and potential justification for continued operation. This will include recommendations regarding potential inspection intervals, risk assessment diagrams based on rotor design and firing temperature, an understanding of the influence of metal part temperature and peak stress on SAGBO, tools for addressing starts-based vs. hours-based approaches and operational strategies to reduce risk.
Task 4 – Technology Transfer. Dissemination of research results will include conference presentations and journal papers on generalized findings to ensure the impacts of the research engage a larger community. All mechanical test data and key details, such as informed risk tools and methods for detailed operational analysis, will only be transferred to funding members of the project. Regular project update meetings delivered via face-to-face or through web-based meeting platforms are expected through the duration of the project.
Deliverables
The expected deliverables from this project may include:
- A materials database
- A framework for conducting an operational analysis to support rotor life extension
- Tools (e.g., spreadsheet or web-based) to evaluate risk associated with life extension
- Guidelines for recommended inspection intervals
Price of Project
The cost to join is $150,000 per funder, which can be spread over a maximum of five years. The project qualifies for self-direct funds (SDF). Funders will have the option to leverage project outcomes to inform a fleet-wide or individual rotor life assessment as an additional supplemental or a billable service agreement (BSA) for a fixed price.
Project Status and Schedule
The project will be initiated after commitments from four supporting funders, with critical mass expected by September 2025. The project will be largely completed over a 36- to 48-month timeframe, pending the overall participation.
Who Should Join
Utility end-users, insurance providers and any supply chain stakeholder directly involved with the operation, maintenance, and management of 6F, 7F, 9F, 7HA and/or 9HA gas turbine rotors utilizing IN706 material should consider joining.
Contact Information
For more information, contact the EPRI Customer Assistance Center at 800.313.3774 (askepri@epri.com).
Technical Contacts
Alex Bridges at 704.560.8709 (abridges@epri.com)
Bobby Noble at 704.614.3746 (bnoble@epri.com)
John Scheibel at 650.855.2446 (jschiebe@epri.com)