Advanced Labs Help Electric Industry Prepare for a Clean Energy Future
EPRI's labs are research and development facilities that go beyond standards testing to include designing new methodologies and evaluating emerging technologies. For example, in our transmission and distribution facilities, we can simulate an entire distribution system and all of the systems and processes from the distribution grid to the end-use customer.
A large collaborative of energy companies, academia, government, and external scientists also inform our research. They bring real-world problems to us, and the results of those tests often have positive impacts for society.
Our expert staff are dedicated to evaluating ideas and breaking new ground to meet the needs of an energy transition that is evolving faster than ever before.
Lab Stations Group Name
138kV Research Substation
Lead: Luke van der Zel
Research substation to investigate component, monitoring, and diagnostic performance.
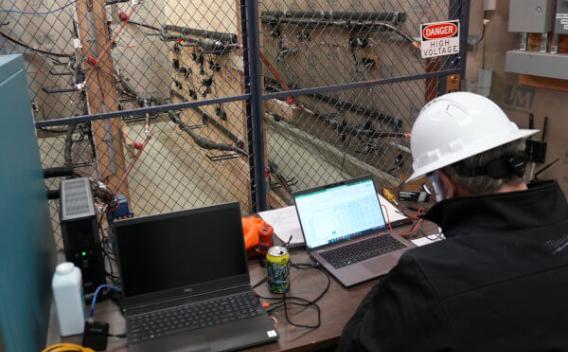
Underground Connector / Cable Accessory Thermal Test Area
Lead: Josh Perkel
This test area is capable of loading underground cable accessories with up to 1,000A of continuous current to simulate the impact of different load profiles on their thermal behavior. The area includes instrumentation for monitoring temperatures via thermocouple and infrared thermography as well as real-time connector resistances.
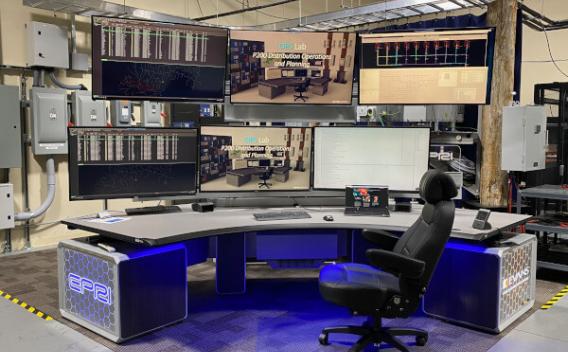
Operations, Protection, Systems (OPS) Lab
Lead: Miguel Hernandez
From the operator to the device, the OPS Lab provides capabilities to emulate a complete distribution system to test protection, control, and automation systems.
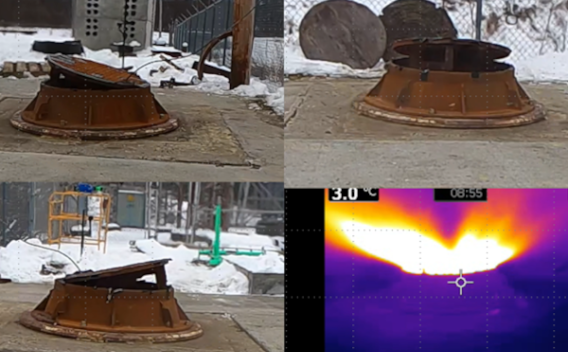
Underground Research Facility (Manhole Test Area)
Lead: Alex Bologna
Full-scale manhole test facility for studying the impact, prevention technologies, and mitigation strategies for manhole explosions. This site has been extensively used in the development of restrained manhole cover and frame systems.
Accelerated Aging Chambers
Lead: Tim Shaw
Computer-controlled environmental system simulates a defined climate inside the aging chamber by varying temperature, clean fog, salt fog, clean rain, UV radiation, and humidity.
UAS Testing
Lead: Dexter Lewis
Drone test site to understand aircraft and payload performance in electric environments.
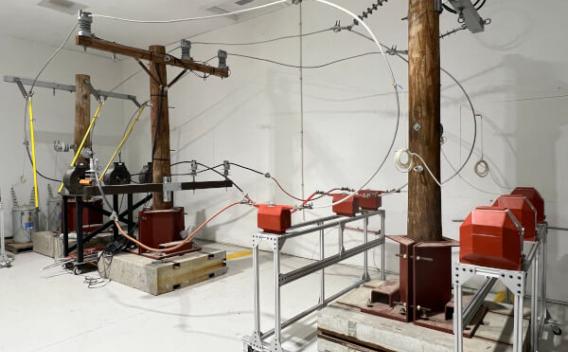
Distribution Automation Asset Testing
Lead: Jason Anderson
Controlled investigative performance testing of automation assets utilizing various withstand equipment and the EPRI Lenox laboratory custom calibrated three-phase wye line segment current loop to inject high voltages of ≤19.9kV and ≤600A to determine 60Hz accuracy of sensors.
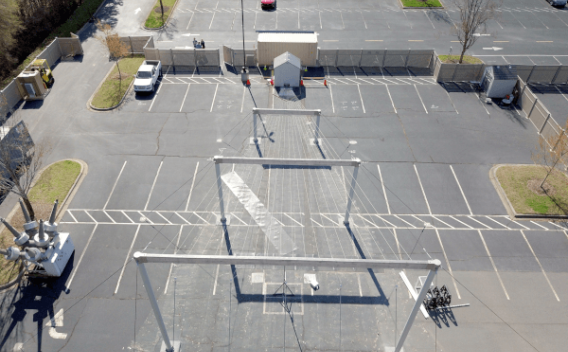
Electromagnetic Pulse Testing
Lead: Charles Perry
Testing substation, distribution, and telecommunications equipment to determine the strength of the equipment when subjected to the radiated and conducted pulses from a high altitude electromagnetic pulse (HEMP) and testing of EMP mitigation technologies such as EMP filters, surge suppression devices, and RF shielding.
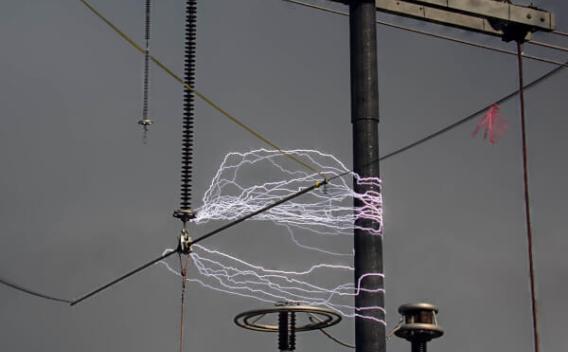
Impulse Testing
Lead: Steve Baker
Three impulse generators are located in the EPRI Lenox laboratory, the largest of which is the 5.6MV tower which simulates lighting and switching surges for performing component testing and insulation coordination mapping.
Full Scale Distribution Structure Testing
Lead: Steven Dulin
Resiliency & reliability testing of full-scale distribution structures using simulated tree strikes and falling branches.
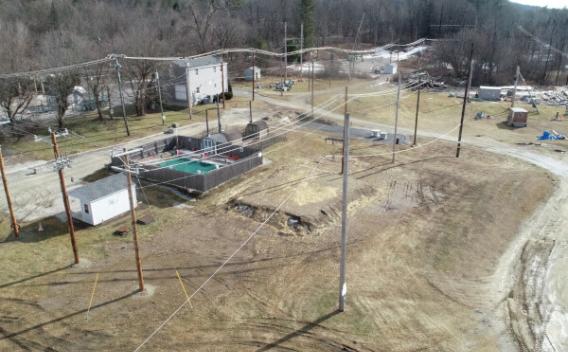
23kV 3-Phase Distribution Test Line
Lead: Ross Barrette
The 23-kV 3-phase distribution test line is a 1-km long line that allows us to test distribution technologies on a more realistic length and geometry. This is particularly valuable for testing downed conductor detection, distribution condition monitoring technologies, and distribution inspection technologies.
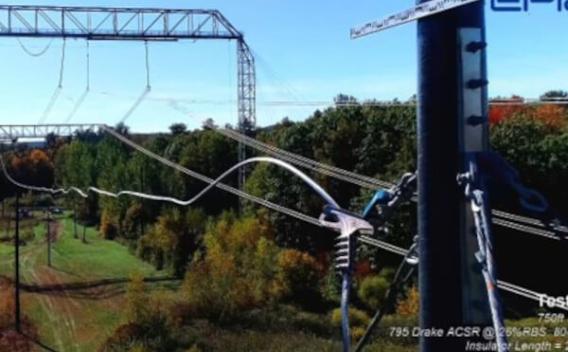
Dynamic Impact Test Line
Lead: David Folk
Simulates broken wire events on a power line system helping utility engineers quantify the dynamic forces that occur during broken wire events, and ultimately design more resilient transmission and distribution structures.
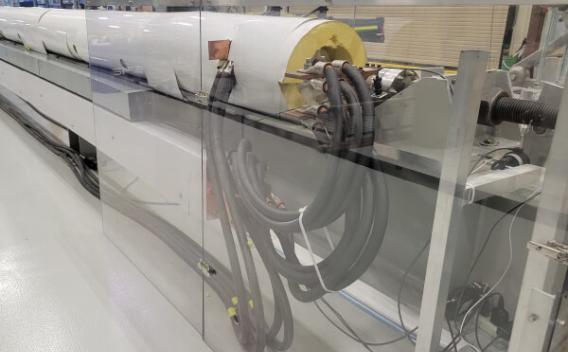
Thermo-Mechanical Bending Rig
Lead: David Kummer
This rig investigates the impact of thermo-mechanical bending on design, operation, and long-term performance of extruded dielectric transmission cables. The test rig incorporates a 55-meter-long sample length of cable installed in a specially designed steel duct to measure the cable end forces, thermal profile, and movement patterns within the duct. Results from this test rig can be used in design, operation, and maintenance of such cable systems.
Stray Voltage Test Site
Lead: Doug Dorr
Facility designed to replicate user defined human and animal perceptible shock scenarios. This includes ability to simulate concerns associated with urban shock hazards, overhead distribution stray voltages and swimming pool electric shock concerns.
Reconfigurable Transmission Line
Lead: Steve Baker
Three phase reconfigurable transmission line more than 500 meters long.
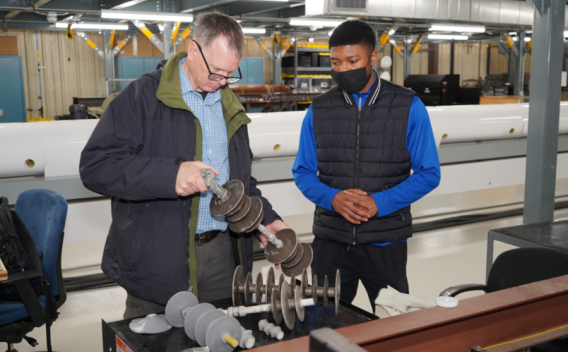
Insulator Testing and Research
Lead: Tim Shaw
Evaluation of aged transmission assets, with a focus on insulators.
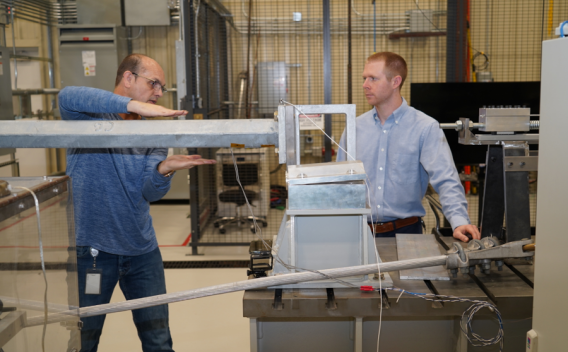
Vibration Rig
Lead: Jean-Pierre Marais
Conductor line and components vibration testing rig.
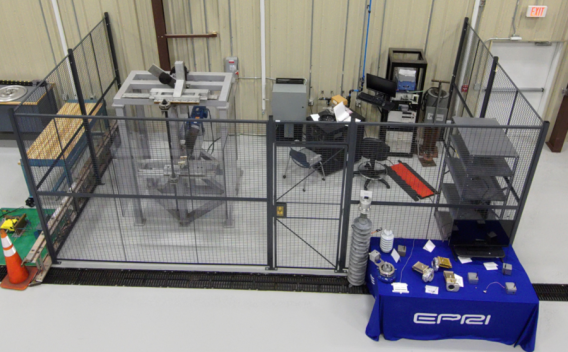
Galloping Rig
Lead: Jean-Pierre Marais
The galloping rig is designed to generate motion (horizontal, vertical, and circular) for accelerated life cycle testing of components.
Advanced Conductor Rig
-
The overhead transmission conductor rig is utilized to perform accelerated thermal mechanical aging of conductor-connector systems. This testing enables EPRI to analyze the degradation and failure mechanisms of overhead transmission conductors, connectors, and attached hardware. Furthermore, inspection techniques and technologies are evaluated and refined.
-
The overhead conductor test rig can hold up to 24, 90-foot conductor-connector test samples under tension. There are six power supplies, each capable of producing 2000 to 3000 amps of current to resistively heat the conductor-connector systems. The test system has the capability to monitor line tensions and temperature during testing.
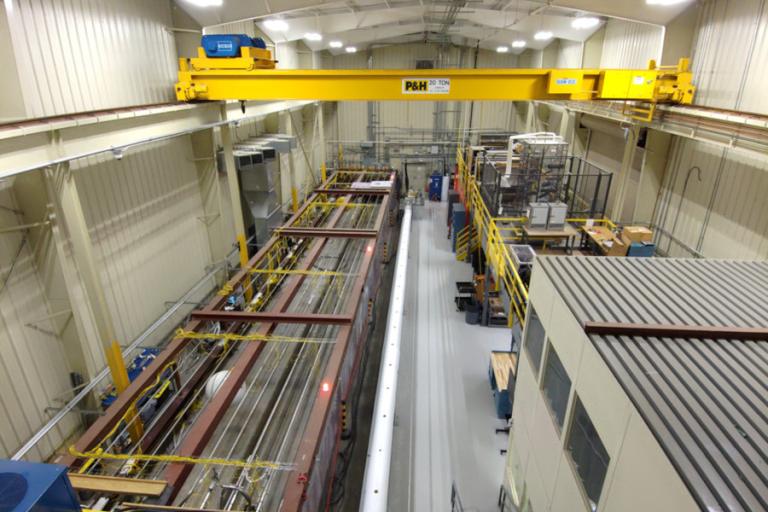
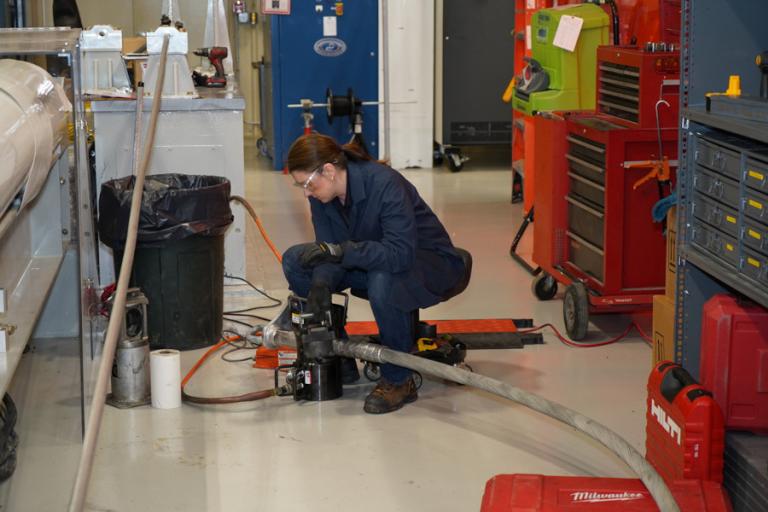
Forensics
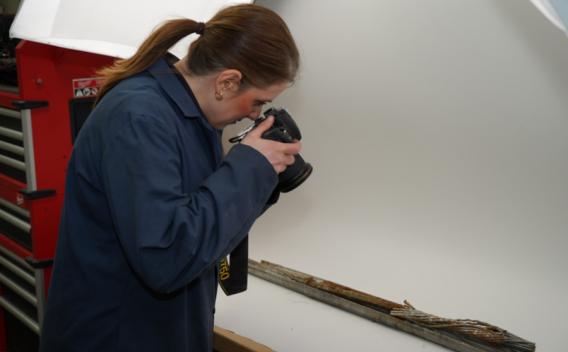
The EPRI Forensics Lab provides space and equipment for analyzing assets to determine degradation and failure mechanisms. The lab is equipped with tools for dissection and measurement devices along with photography lighting and camera equipment. Microscopes provide researchers with the capability to examine fine details of samples. High-resolution images are taken of samples for documentation and technical transfer to members.
Distribution Automation
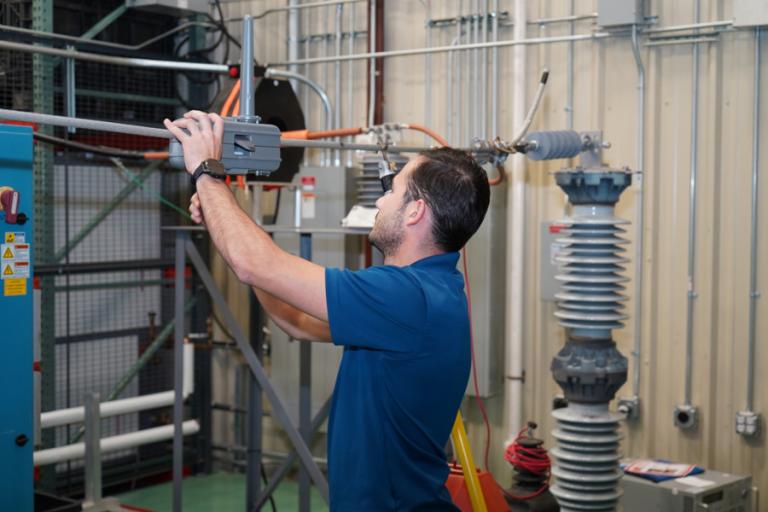
The environmental chamber and test cage are used to test sensors at different voltages, currents, temperatures, and humidity levels.
MV Voltage Supply – The medium voltage applied to the test loop is created by back feeding an instrumentation transformer using a BK Precision Programmable Power Supply.
Test Loop Current Supply – The test loop current is created by back feeding a current transformer using an ELGAR Programmable Power Supply.
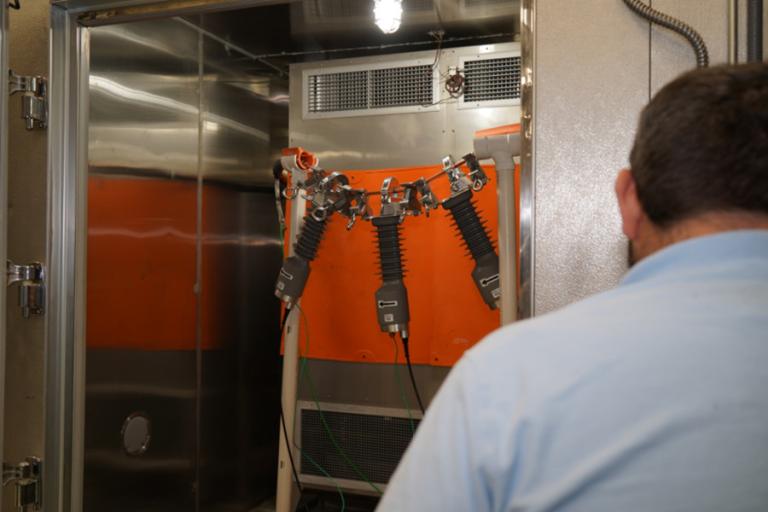
Thermal Mechanical Bending Rig
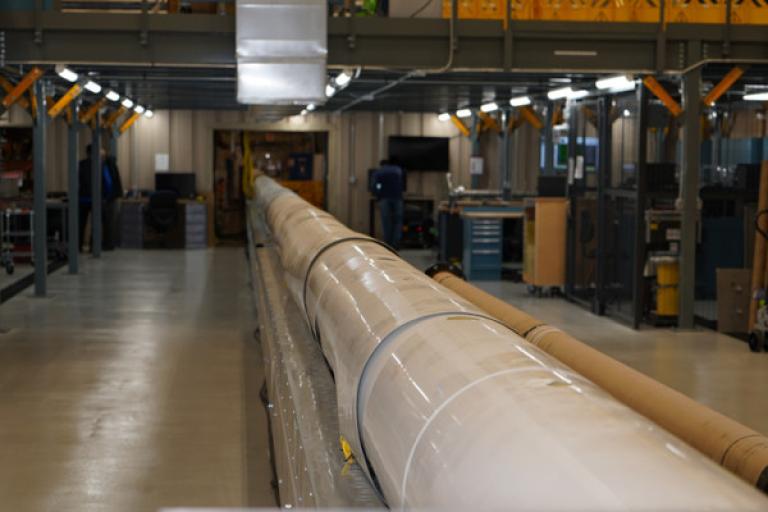
The underground transmission TMB rig is used to test the thermo-mechanical forces on extruded cables installed in a duct. The test applies a DC current to heat the conductor and sheath of a 55-meter-long extruded cable installed in steel duct. The test monitors the end forces, temperature, and cable position, as well as the sheath and conductor current and voltage outputs for the duration of the test.
Arc Flash / Arcing Fault Testing
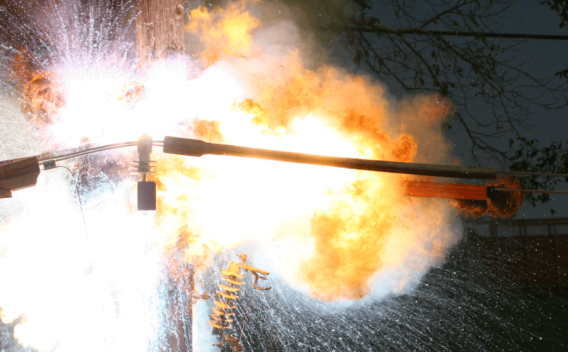
Lead: Tom Short
Evaluate the impacts of faults and arcing with up to 3000A. Testing has evaluated:
- Arc flash
- Burndowns of bare and covered conductors
- Tests of arc-fault protectors to prevent burndowns
- Flammability of equipment under fault conditions
- Damage to crossarms and insulators under fault conditions
- Performance of sensors during faults
- Grounding and stray voltages; step and touch voltages during faults
- Evaluation of vegetation faults
- Fuse cutout and single-phase recloser performance
- Fault-induced conductor slap
- Wildfire ignition