Background
American Electric Power (AEP) has made several applications of advanced conductors over the past 10 years, for 138–345 kV (Table 4). These projects have predominantly been involved in increasing capacity into existing load areas. The upgrade alternatives were limited on these projects because they largely were constrained by urban growth and the inability to secure additional rights of way for new lines. The economics of reconductoring lines on existing corridors primarily focus on whether the existing structures can support the new conductor(s) required for the target capacity and whether the structure heights with the new conductor provide adequate clearance. For HTLS conductors, this is a prime target opportunity for a solution. The examples will expand details of these projects.
Table 4. AEP examples of ACCC installations
Project | Voltage | Amount of Conductor | Installed |
---|---|---|---|
Leon Creek, Pleasanton, Texas | 138 kV | 259,200 ft | May 2006 |
Chambers Spring, Tontitown, Arkansas | 161 kV | 203,400 ft | January 2007 |
Bluff Creek, South Abilene, Texas | 138 kV | 319,900 ft | March 2007 |
Flint Creek, Centerton, Arkansas | 161 kV | 363,200 ft | March 2009 |
Riverside, Glenpool, Oklahoma | 138 kV | 35,500 ft | March 2009 |
LRGV 345-kV energized reconductor, Texas | 345 kV | 7,603,200 ft | November 2015 |
1 ft = 0.3 m
LRGV = Lower Rio Grande Valley
In the San Antonio, Texas, area, AEP shares a line with City Public Service (CPS), the San Antonio municipal electric utility. CPS had recently rebuilt its portion of the line with a larger conductor, Drake ACSR. AEP’s strategy was to use the existing corridor and structures as much as possible while providing the equivalent capacity to CPS’s design. The advanced conductors offered AEP several options to meet this criterion. Minimizing structure replacements would mean a shorter project time, which represented saved dollars, as well as mitigating structure replacement costs. Optimizing the value of the existing corridor assets was also an objective that AEP carried throughout its system.
Options Evaluated
After reviewing several different advanced conductor offerings by various manufacturers and assessing the alternative sizes and project solutions, AEP chose to investigate ACCC/TW further. The trapezoidal shape of the TW strands enabled increased capacity in the same effective conductor diameter. AEP was concerned with the new technology of a single composite core as the primary, near sole, mechanical strength component. After reviewing the different laboratory test data provided by CTC and General Cable and results of EPRI’s testing of HTLS conductors, AEP became comfortable with the risk of applying the ACCC HTLS conductor (Figure 22). The estimated cost savings of using the HTLS conductor over and above the premium for the conductor were $600,000 (USD), largely attributed to minimized structure modification/ replacement costs. The resulting configuration provides a 75% increase in line capacity.
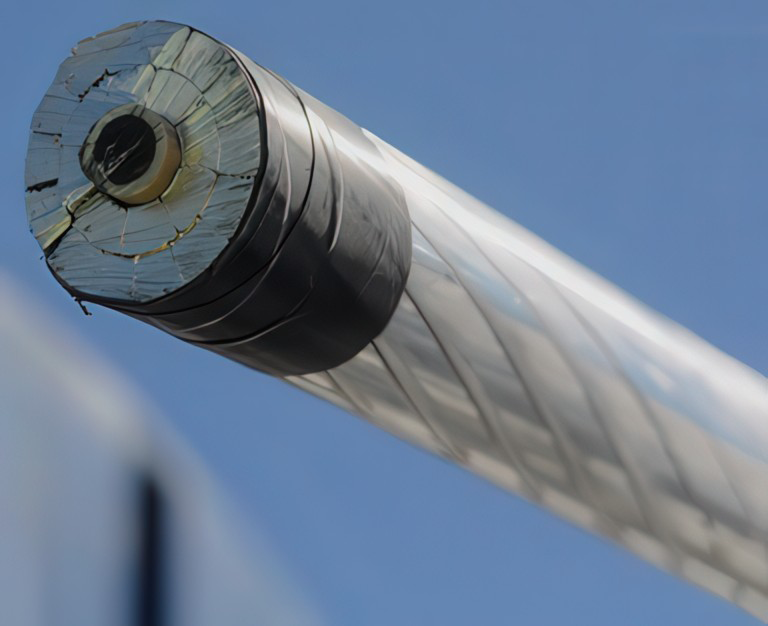
Figure 22. Close-up of an ACCC construction
Installation: Lessons Learned
Installation of the ACCC was routine, beyond three core breaks that occurred during stringing. The first incident was in the very beginning of the operation and was attributed to operator error of the stringing puller. Rather than applying the brake, the wheel was left to run free, and slack developed on the bull wheels; the conductor jumped the wheel-track and ended up on the axle. The conductor stress that developed around the small radius of the axle caused the core strand to rupture.
The two subsequent failures ultimately were attributed to rough handling during stringing, although specific incidents or factors could not be identified. A thorough assessment of the chemical and mechanical properties of the conductor and core strands of the damaged wire and new wire was performed and compared to specifications. No deviations from specifications were found in either sample set. The reels from the impacted conductor were set aside and new reels installed. No further issues from these conductors have occurred during stringing or operations.
The stringing guidelines provided by the conductor manufacturer were re-emphasized and trained across all involved parties. Close attention to recommended stringing practices must be applied.
Energized Reconductoring Project
AEP also selected ACCC conductors for a large 345-kV project in the Lower Rio Grande Valley (LRGV) area of Texas. Large load growth, a reduction of local generation sources, and the introduction of renewable energy resources prompted the need to increase the capacity of several lines into the LRGV area. The same driving forces that justified the need for the projects also created a significant construction constraint—no outages for reconductoring. This meant that the existing structures had to support the new conductors mechanically and provide adequate clearance without structural modifications. AEP’s experience with ACCC, covered previously, led to another solution opportunity. Another benefit of the ACCC conductor is its resistance to environmental factors, which, in the case of the LRGV projects, was salt corrosion from proximity to the coast.
The tubular steel H-frame lines were reconductored with the line energized (Figure 23). Novel boom truck attachments provided temporary supports to the conductors while a single-phase bypass line was erected to support a phase while it was being reconductored. The conductor was not energized during the stringing operation; all work was done in very close proximity to the other energized phases on the structure (Figure 24). The project was completed in November 2015 and was considered the largest single installation of an advanced conductor in the United States. Due to the size of the project and the energized work method used, the project was awarded the Edison Award by the Edison Electric Institute in June 2016 and was featured in several trade magazine articles.
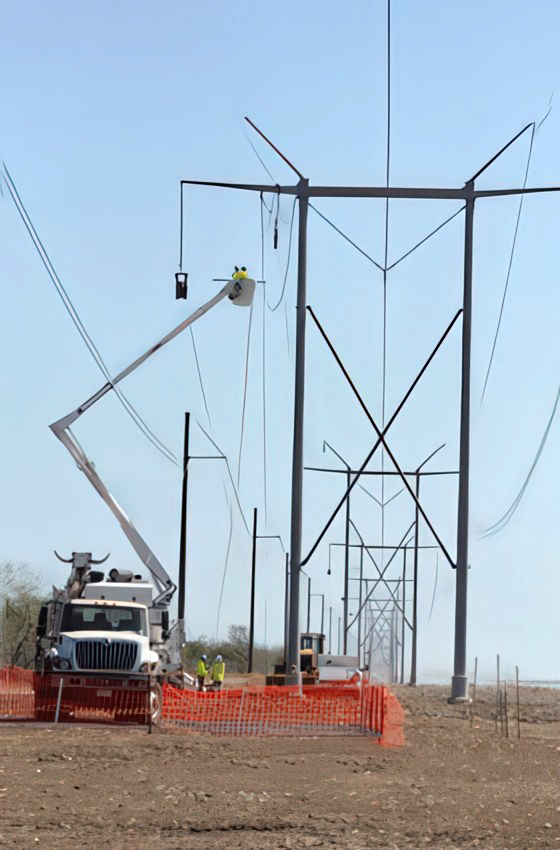
Figure 23. Typical structure type
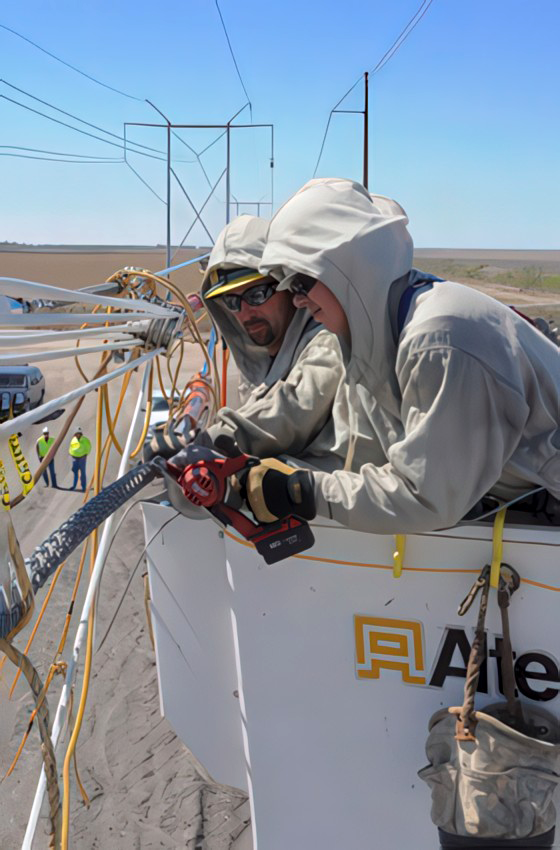
Figure 24. Aerial splicing