TIWAG-Netz AG, ZTACIR Alps Reconductoring Application
Project Description
In a paper presented to CIGRÉ General Conference in 2012, TIWAG-Netz AG discussed its development of a reconductoring project using the ZTACIR conductor.2 An 85-km-long 220-kV line (over 50 years old) across the Alps had been experiencing several maintenance and reliability issues (inability to maintain N-1 criterion and excursions above the conductor’s thermal limit). Also, load growth and emerging distributed generation through renewables made impacts on the long-term planning and operating requirements. The result was that the utility considered long-range and interim solutions.
Options Considered
As mentioned, the long-term growth and system requirements indicated that, ultimately, a new line would be required. Options of 220 kV with larger capacity conductors and 380 kV were considered. The time delays for securing a new line route and commissioning a new line would not, however, solve the current issues with meeting N-1 criterion and load requirements for the existing line. An interim solution had to be developed to address grid requirements soon. Near-term solutions included load flow control through series reactors or the application of high thermal limit conductors. Ultimately, the high thermal limit conductor provided the greater capacity of the two options and was pursued.
Justification for HTLS Selection
Concerns about the losses that would be incurred through the high current loads were studied. For the ZTACIR conductor being studied, resistance rises proportionately to the increase in operating temperature and the projected losses are approximately five times what they are for the nominal 80°C level when operating with 90% more load at a conductor temperature of 180°C. However, load monitoring of the line at several substations indicated actual load flows were not at the maximum capacity of the line but much lower, making the potential level of losses a minimal impact. The capacity required was for meeting N-1 constraints during outages, planned or forced—that is, short-term situations and not nominal load levels.
A more significant concern with accepting the potential of such a heavily loaded line of this length was the reactive power demand of the line, as depicted in Figure 46. Because the reconductoring option was intended to maintain the original structures and line geometry, the nominal reactive load of the line was reduced from 180 MW to 120 MW, characterized by using one conductor rather than a typical bundle for 220 kV.
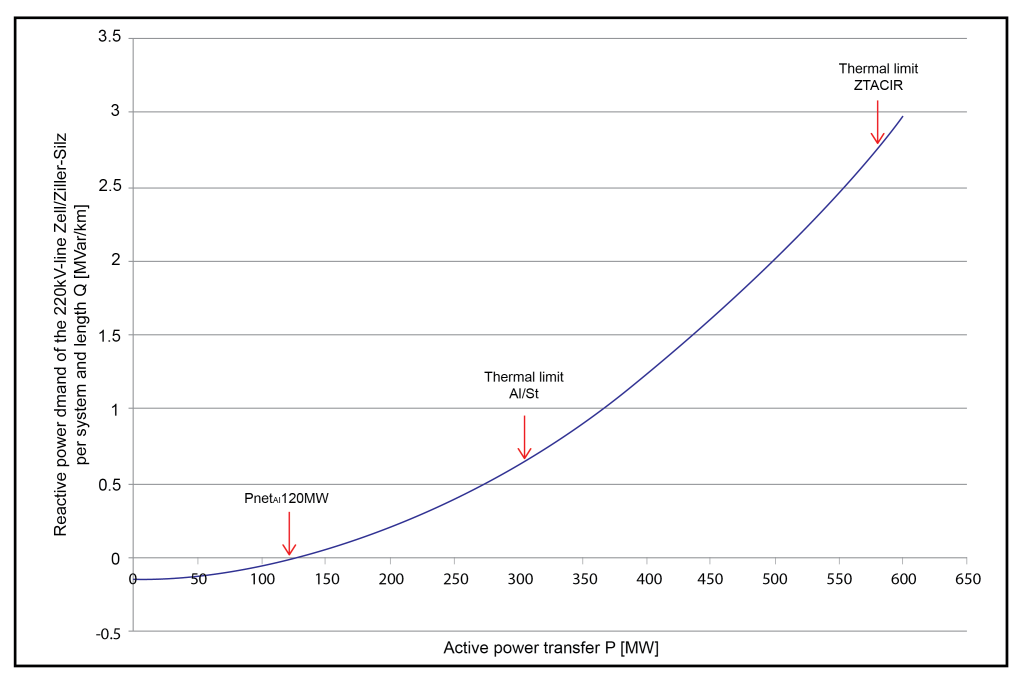
Figure 46. Reactive power demand online
The conductor selection required using a conductor of the same size: diameter and unit weight per foot as the existing conductor to minimize impact on the structures. In addition, the maximum clearance could not be less than the original conductor position at its MOT of 80°C. The limits for electric and magnetic field levels along the line also had to keep previous limits.
The ZTACIR conductor could meet these requirements. The aluminum alloy strands can withstand the continuous 180°C operation; the Invar strands in the steel core dealt with the sag limitation by elongating less with the rise in temperature. In addition, it was decided to apply a temperature-resistant black coating on the outer surface. Even though the coating would raise the solar radiation heat level of the conductor when under 60°C, it would have improved heat radiation properties at the maximum operating levels, which would effectively help lower the conductor temperature. Finally, the fact that the ZTACIR installs the same as conventional ACSR made its application attractive. Table 7 contains a comparison of conductor parameters between the existing conductors and the proposed ZTACIR.
Table 7. Conductor parameter comparison of ZTACIR and an in-service conductor
Overall Diameter (mm) | Weight (kg/m) | Cross- Sectional Area (mm2) | Rated Tensile Stress (daN/mm2) | Current-Carrying Capacity (amps) | Max Temp (°C) | Rate of Thermal Expansion (1/°C×10-5) */** | Elasticity Modulus (daN/mm2) */** | |
---|---|---|---|---|---|---|---|---|
ACSR 341/109 | 27.7 | 1.799 | 450.0 | 41.68 | 807 | 80 | 1.67 | 8400 |
ZTACIR 341/109 | 27.7 | 1.721 | 450.0 | 38.29 | 1572 | 180 | 1.412/0.342 | 7842/14,912 |
*/** ≤ transition point/≥ transition point.
Installation Review
A utility requirement was that compression connectors were to be designed so that the connectors would never exceed 90°C with the conductor at full load. Further, there was a concern that excessive temperature excursions could loosen the mechanical bolted clamps at suspension points. To maintain a temperature of 55°C or lower at the attachment points, an additional layer of armor rods was installed at suspension points.
Because there are no connector standards currently available for high-temperature operation, a series of tests were performed on proposed fittings for the ZTACIR conductor. Heat cycle tests defined in CIGRÉ TB 426 were carried out. The specified minimum failure load (SMFL) test was conducted not only at room temperature but also after a length heat cycle hot/cold and with extreme temperature applied, hot. The two test cycles are shown in Figure 47 and Figure 48.
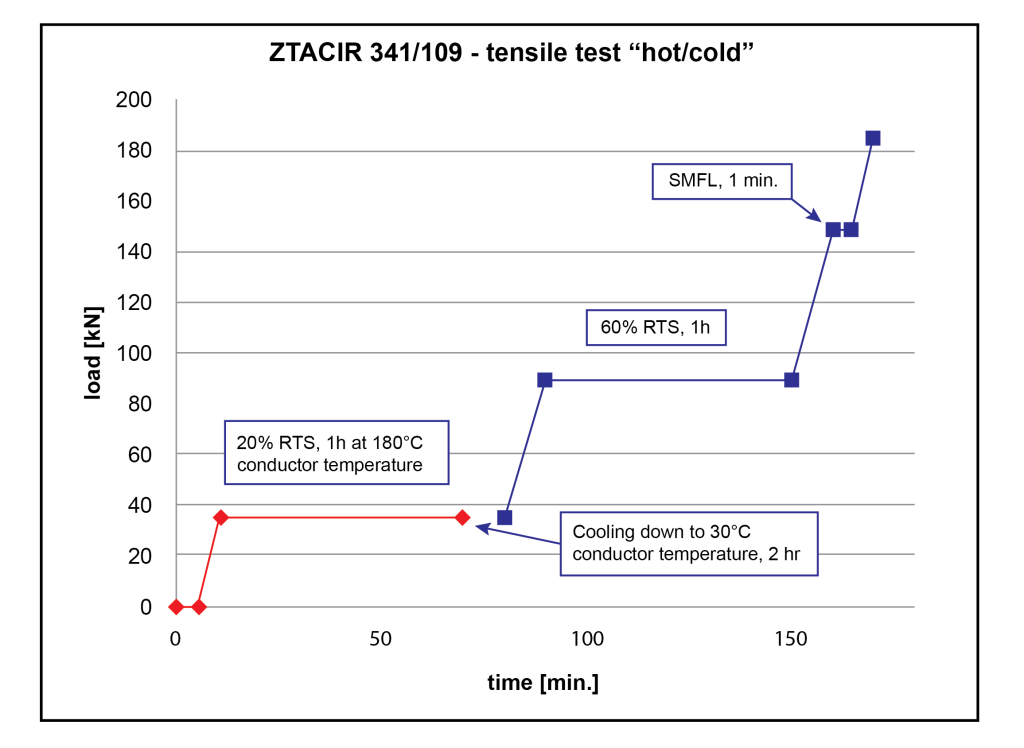
Figure 47. Time-stress-temperature run—tensile test hot/cold
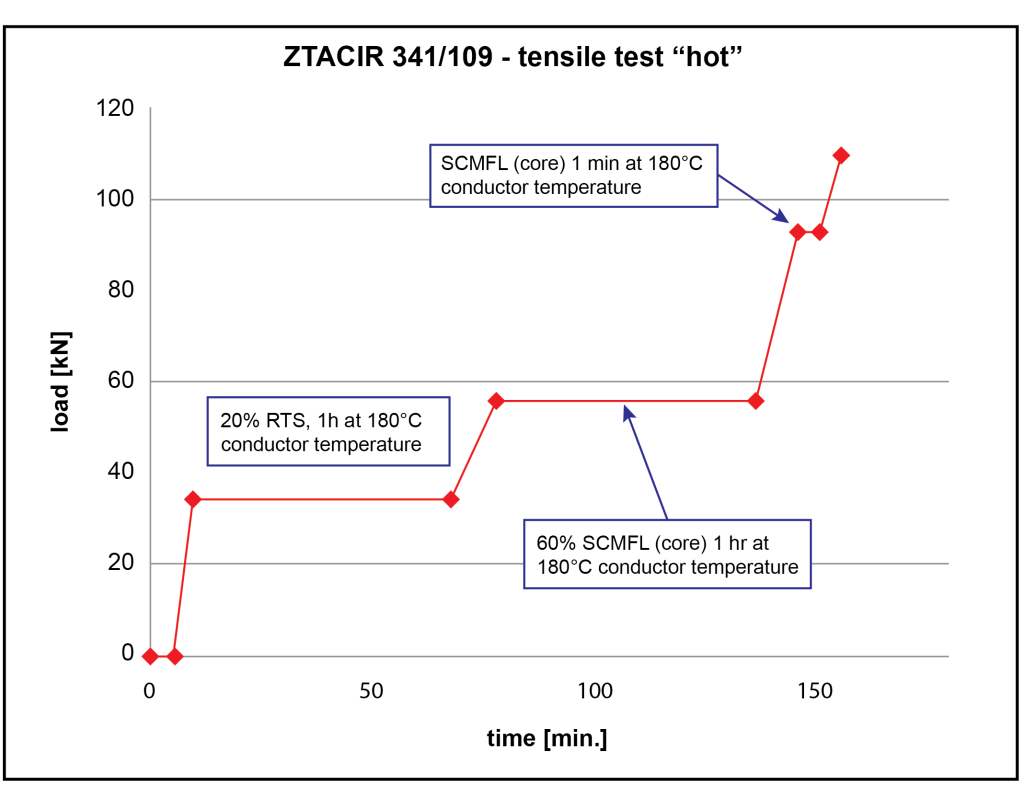
Figure 48. Time-stress-temperature run—tensile test hot
The test showed that the performance of the conductor systems is very dependent on the fittings and their installation. Furthermore, the behavior of the system, its sag performance, is dependent on accurately characterizing the conductor parameters and following through on their installation. The pre-stressing of the conductor showed a significant impact on defining the transition point for the core to alumina strand relationship. The right chart in Figure 49 indicates the shift in the transition point under different pre-stress levels.
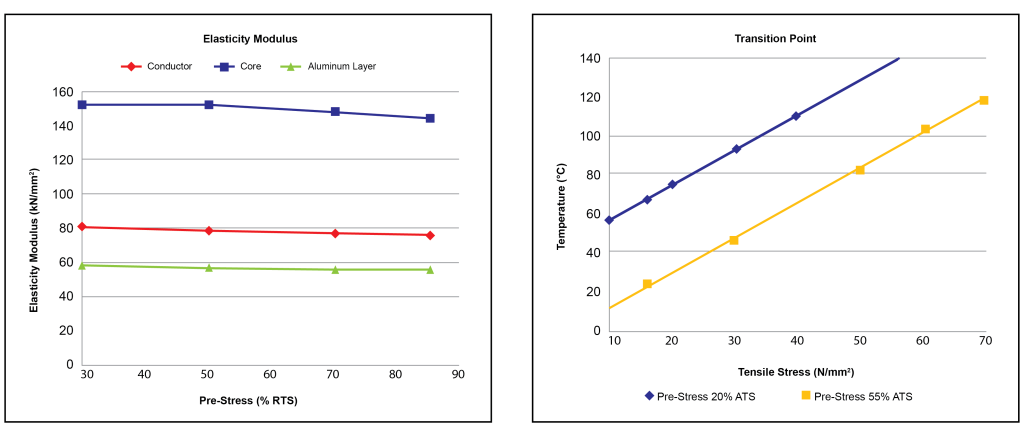
Figure 49. Transition point and elasticity modulus for the ZTACIR 341/109 conductor
Although the pre-stressing was critical to the overall behavior of the conductor system, it was also a complication in the installation process because many structures could not withstand the pre-stressing tensions due to locations and terrain. Ultimately, a preload of 55% held for one hour was used for pre-stressing the conductor. During the process, measurements and observations indicated that no further creep occurred after 20 minutes (Figure 50). The pre-stress hold was reduced to 30 minutes.
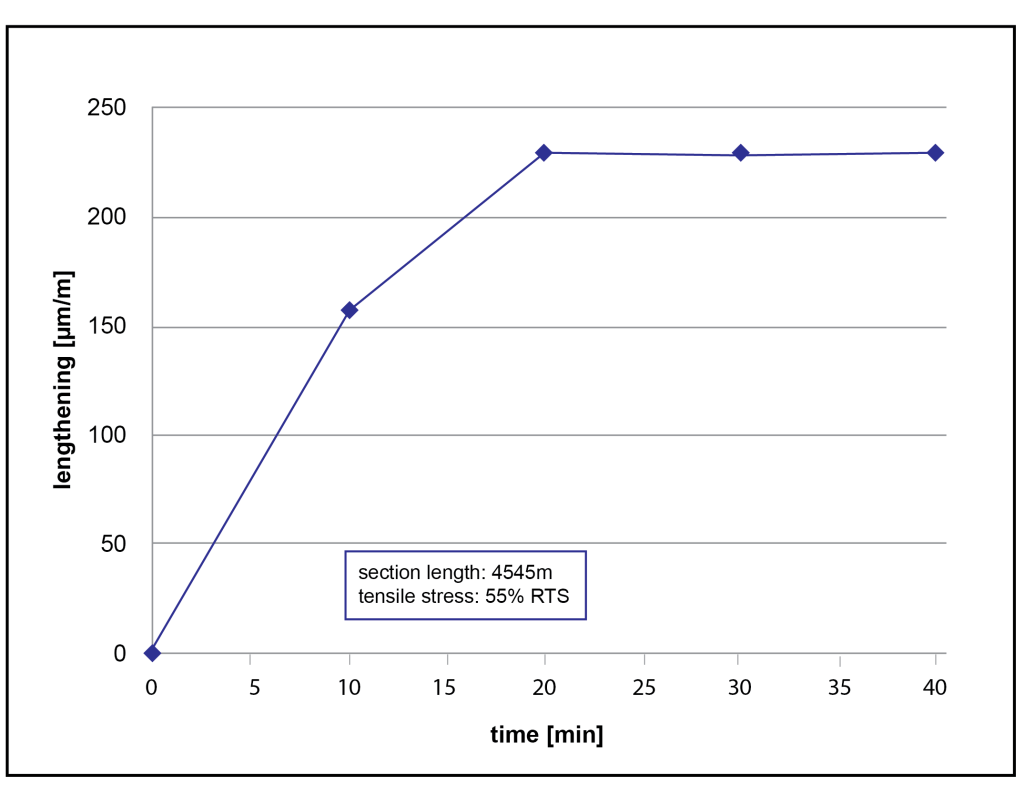
Figure 50. Conductor elongation under pre-stress
2 Bodner, J., Höffer, M., Lauβegger, M., Stampfer, G., Strobl, H., and Wörle, H. “Use of High Thermal Limit Conductors in the Replacement of 220 kV Overhead Lines in the Tirolean Alps.” CIGRÉ: B2-103. 2012.