Project Description
Avista utilities identified a need for increased capacity in the area around Spokane, Washington. Load growth and the need to provide access to a more diversified mix of generation lead to potential overloads on a 70-year-old 115-kV line. Avista has been carrying out a progressive enhancement and upgrading program across their infrastructure with numerous environmental, regulatory, financial, and landowner constraints driving broader solution evaluations and engineering decisions.
A recent project involved the Ninth & Central and Sunset 115-kV line, originally built in the 1940s, using a 250-kcmil copper conductor on wood poles on a right of way that originally had been in a rural locale but since transposed to a highly mixed-use residential and commercial area. In addition, a section of the line was in an environmentally sensitive area that would require access by helicopter and hand-tooled work rather than access to the ground and mechanized installation. Collectively, the solution would require Avista to stretch outside of its box of conventional construction methods and technology applications.
Options Considered
To meet the increased capacity requirements, Avista did an extensive study of conductor types and sizes available. A portion of the line had already been upgraded with the 795-kcmil AAC. The AAC required shorter span lengths than Avista wanted to apply on the rest of the line. Rather than substituting a similar sized ACSR conductor, Avista studied a variety of different ACSR sizes and other stranding types. The optimum ACSR size was determined to be a 1272-kcmil Bittern ACSR, which Avista had applied on several projects.
Avista had also applied ACSS on previous projects and understood its ability to provide increased capacity while minimizing structural requirements. Initially, it selected an ACSS 795-kcmil Drake for the upgrade. Avista completed the upgrade design using the Drake ACSS construction.
During the design of the upgrade, Avista investigated the application of General Cable’s E3X Technology. The E3X Technology is a thin, durable coating on the exterior strands that changes the absorptivity and emissivity of the aluminum strands, allowing the conductor to operate at a cooler temperature. The increased emissivity and reduced absorptivity allow the conductor to dissipate more heat and gain less heat from solar radiation. Keeping all Avista’s other rating parameters the same, the E3X conductor can carry 15% more capacity than the same conductor without the coating. Another advantage of the conductor coating system is that the same hardware and stringing conditions are compatible with the uncoated conductor. Only additional wire brushing during installation of connectors, dead-ends, and splices is required.
Figure 31 provides a comparison of the available ratings for the different types and sizes of conductors considered during the Avista conductor selection study.
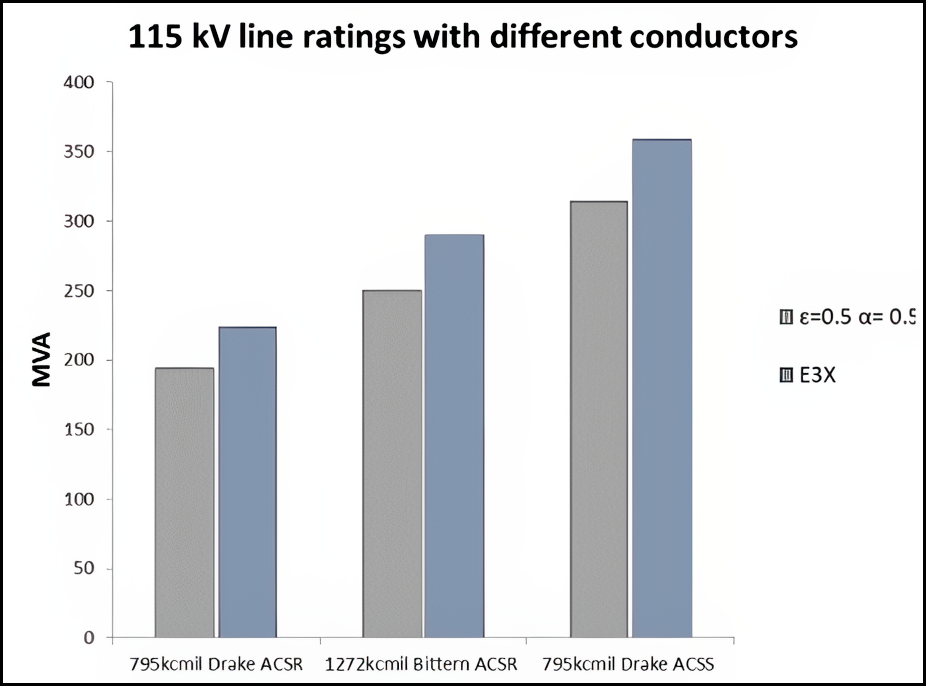
Figure 31. Ratings comparison for different sizes and types of conductors studied
Conductor Selection Justification
Avista had already selected and designed the upgrade for the ACSS conductor by deciding on the line. Because the technology involves only a coating on the outer strands of the conductor, the structures being designed for the ACSS conductor, and all the hardware and insulator assemblies, did not require any modification. The E3X conductor provided an additional 15% capacity at less than a 1% increase in the project cost.
One of the drawbacks of standard ACSS is higher losses due to the higher conductor operating temperature. By allowing the conductors to run cooler for any given load, E3X technology also helps lower line losses and increase efficiency, especially as the conductor becomes more heavily loaded during peak demand. For example, a power flow that pushes a standard ACSS conductor to 200°C can operate at approximately 150°C with E3X for the same load. This cooler temperature lowers line losses by approximately 20% when the line is heavily loaded—another benefit that, in addition to the 15% higher line ratings, easily outweighed the increase to the total project cost. In keeping with Avista’s commitment to being a good steward and a good neighbor, E3X technology also dulls the surface finish of the conductor, like a non-specular conductor, reducing the visual impact compared to a typical shiny new aluminum.
Although the decision to deploy E3X technology was made easy by the culmination of several benefits, Avista also did its due diligence in making sure that the technology was proven. First installed and energized on utility lines in late 2013, conductors with E3X technology have been tested to stringent protocols and evaluated through extensive validation in field trials and customer deployments. The technology has been installed and tested by independent test laboratories, such as Kinectrics and Oak Ridge National Laboratory, and continues to be validated though installations in climates around the world.
Installation Review
Construction was completed on portions of the line with nominal accessibility. The line section that requires helicopter support is scheduled for installation in the near future. The existing line was rebuilt using a combination of single pole steel structures, as shown in Figure 32 and Figure 33, in narrow easement areas and along the road, and steel H-frame construction.
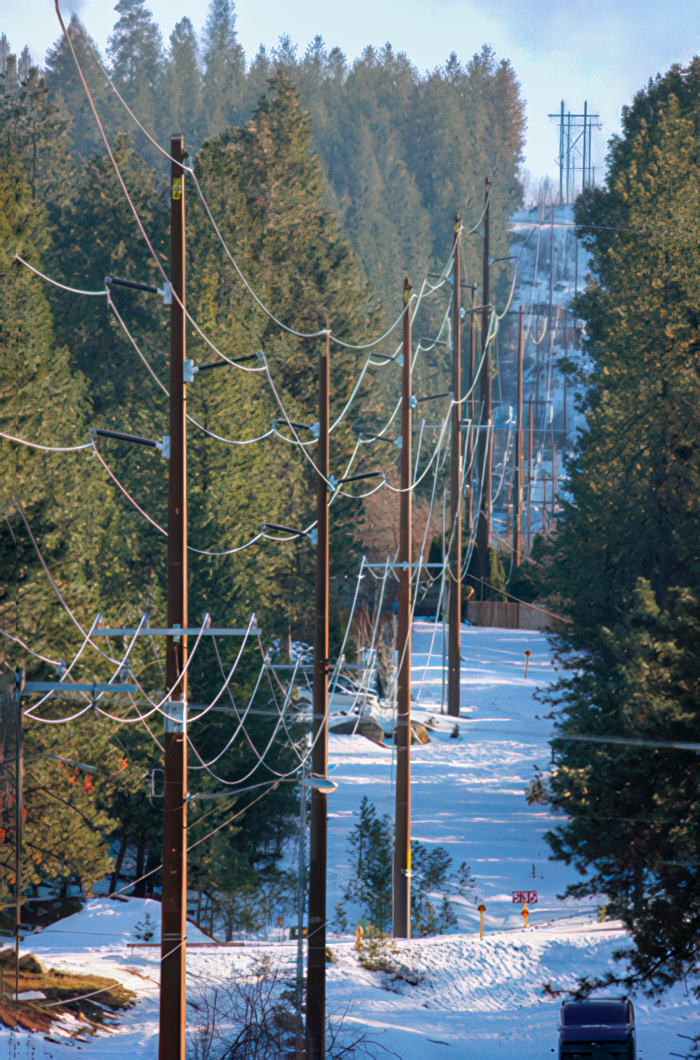
Figure 32. Narrow right-of-way construction on a single pole
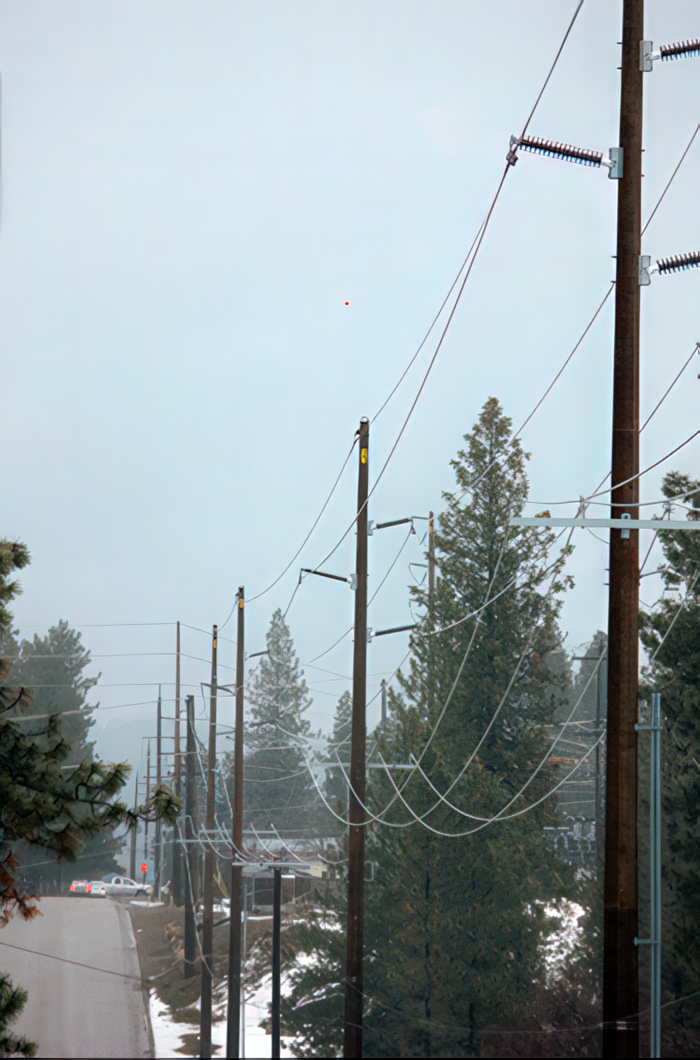
Figure 33. Rebuild along a residential street