Application of ACFR Conductor
Background
CEMIG in Brazil tested several HTLS conductors in an R&D project. The ACFR conductor was installed in the span between Towers 13 and 14 of the double-circuit, 138 kV between Neves 1 and Neves 2 substations, in August 2019. The original configuration of the line has single 170,6 MCM ACSR Linnet conductors providing capacities of 150 MVA at 138 kV. The line length is approximately 13.97 km.
The selected conductor for the research was the ACFR T-Linnet 219.6 MCM. Table 9 shows the comparison of characteristics.
Table 9. Comparison between ACSR Linnet and ACFR T-Linnet
Characteristics/Properties | ACSR Linnet | ACFR T-Linnet |
---|---|---|
Cross-section area (mm2) | 198.4 | 245.9 |
Stranding design | 7 × 2.25 mm – steel core 26 × 2.89 mm (Al 1350) |
7 × 2.27 mm – carbon fiber core 26 × 2.89 mm (Al 1350) |
Nominal diameter of core (mm) | 6.75 (steel) | 6.80 (carbon fiber) |
Nominal weight of core (kg/km) | 217.0 | 44.0 |
Nominal diameter of conductor (mm) | 18.31 | 18.29 |
Nominal weight of conductor (kg/km) | 689.9 | 655 |
Rating (A) (temperature 25oC, wind speed 1 m/s, with sun) | 587 @75oC | 1.050 @150oC |
Rated strength (kN) | 62.9 | 72.5 |
Sag (max. operational temperature – span length 390 m – loading 13.4 kN) |
13.4 | 13.4 |
Justification for Selection of HTLS Conductor
The proposed project was focused on researching different options of HTLS conductors to provide knowledge of advanced conductors for alternatives of uprating urban lines to the company. In addition to the ACFR, a GZTACSR and an ACCC conductor were also installed in other 138-kV lines by the same internal line crew. For this project task, the company decided to replace the Linnet ACSR with a correlated ACFR-T Linnet (Figure 52).
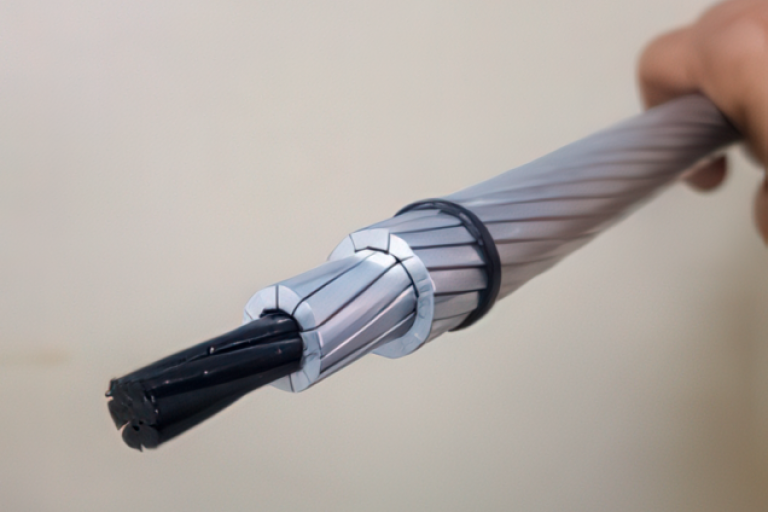
Figure 52. Alubar aluminum conductor fiber reinforced (ACFR) conductor
Installation Comments
As mentioned before, the installation service was executed by an internal line crew that had already installed a section of GZTASCR in the 138-kV Barreiro 1 – BH Bonsucesso and an ACCC conductor in the 138-kV lines Barreiro 1 – Nova Lima 7 and Nova Lima 1 – Nova Lima 7. With the gained experience by the same line crew installing three different options of HTLS conductors, the crew adapted itself easily to the ACFR installation. A highlight point mentioned by the team was that the procedure adopted for the ACFR installation is almost the same adopted for ACSR conductors, except for a slight difference in fittings that are longer and the tension clamp that has an aluminum tube to protect the carbon core (Figure 53). The similarities in installation procedure are reflected in a flexible pulling procedure and consequently in gain in the time of execution (Figure 54).
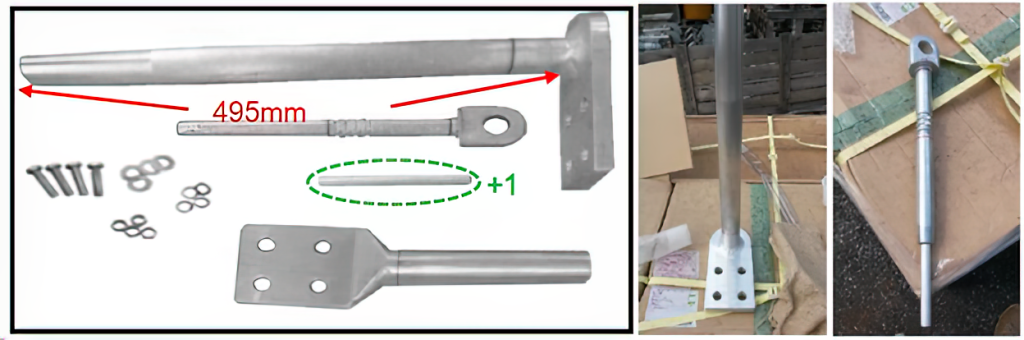
Figure 53. Details of the dead-end connection provided by the conductor manufacturer
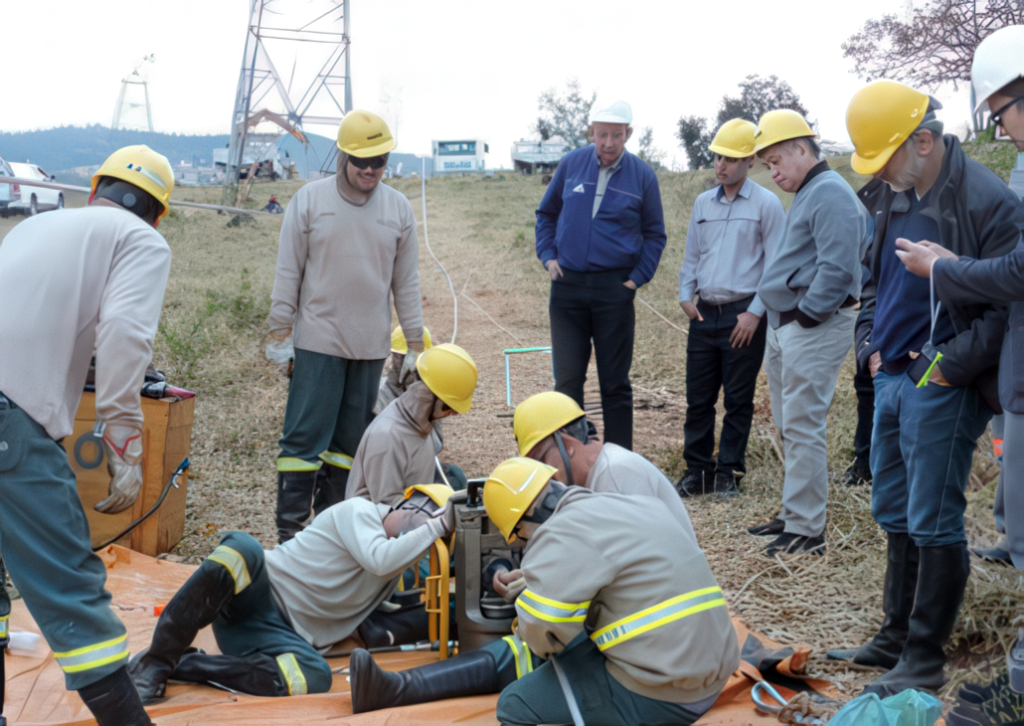
Figure 54. Splice connector compression during an ACFR conductor installation
The installation was planned to be done exclusively by the tension method used with the old ACSR conductor as a pilot to pull the ACFR conductor. The upper phase conductor was puller tensioned. However, due to problems with the puller equipment, the middle and bottom phase conductors were installed with the slack method (Figure 55): dragging the conductor along the ground with protections on obstacles.
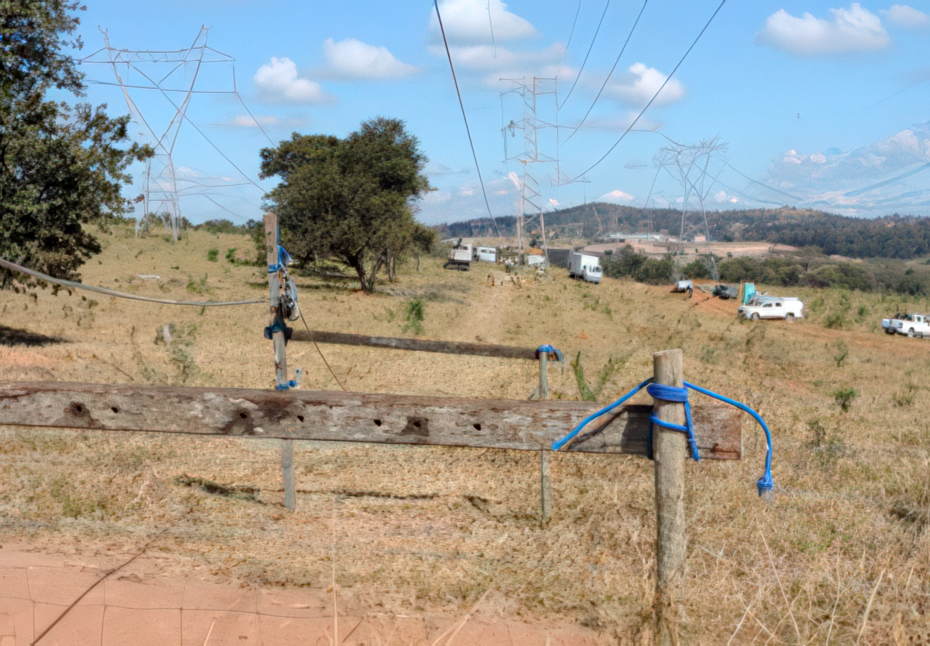
Figure 55. Installation using the layout method of the bottom phase conductor
Application of GZTACSR Conductor
Background
In the same R&D project mentioned before, CEMIG in Brazil installed a GZTACSR-type conductor in the double-circuit, 138-kV Power Line 2 Barreiro – BH Bonsucesso, in 2008.
The GZTACSR was installed in one of the double-circuit power lines. The original configuration of that line has single 477 MCM ACSR Hawk conductors at 138 kV. The line length is approximately 2.1 km.
The selected conductor for the research was the GZTACSR 240 mm2. Table 10 shows the comparison of characteristics.
Table 10. Comparison between ACSR Hawk and GZTACSR conductors
Characteristics/Properties | ACSR Hawk | GZTACSR 240 mm2 |
---|---|---|
Cross-section area (mm2) | 281.14 | 279.6 |
Stranding design | 7 × 2.68 mm – steel core 26 × 3.44 mm (Al 1350) |
7 × 2.4 mm – steel core 15 × 3.46 mm – (trapezoid wire) 10 × 3.69 mm – (trapezoid wire) |
Nominal diameter of core (mm) | 8.04 (steel) | 7.2 (steel) |
Nominal weight of core (kg/km) | 307.3 | - |
Nominal diameter of conductor (mm) | 21.8 | 20.6 |
Nominal weight of conductor (kg/km) | 974.5 | 955.9 |
Rating (A) (temperature 25°C, wind speed 1 m/s, with sun) | 739 @75°C | 1.255 @170°C |
Rated strength (kN) | 85.3 | 86.8 |
Justification for Selection of HTLS Conductor
The purposed project was focused on researching different options of HTLS conductors to provide knowledge of advanced conductors for alternatives of uprating urban lines to the company. In addition to the GZTACSR, an ACFR (previously stated) and an ACCC conductor were also installed in another 138-kV line, by the same internal line crew. The research evaluated options of ZTACIR and GZTACSR conductors for this line but, due to the higher cost and unavailable option of conductor diameter, the project opted for the GZTACSR conductor (see Figure 56).
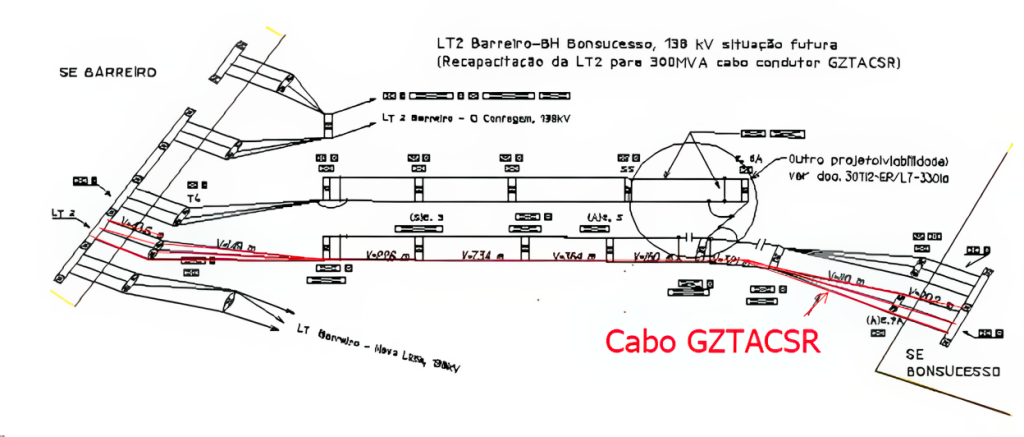
Figure 56. A 138-kV circuits diagram between Barreiro and Bonsucesso substations (uprate circuit in red)
Installation Comments
As mentioned in the previous CEMIG case of ACFR, the installation service was executed by the same internal line crew that installed a section of ACFR in the 138-kV Power Line Neves 1 – Neves 2 and an ACCC conductor in the 138-kV Power Lines Barreiro 1 – Nova Lima 7 and Nova Lima 1 – Nova Lima 7. This conductor installation had some particularities that made the erection technique complex. During the conductor handling, additional care was taken with the steel core that could slide to the inside of the gap.
Another important aspect was the tension and sag regulations of the spans by the steel core to guarantee conductor performance. Since the steel core is covered with a high-temperature grease, the conductor preparation for dead-end fittings’ installations generated a lot of dirt.
Another difficulty was the erection procedure of dead-end fittings since the steel core and the aluminum crimping cannot be done in sequence because the conductor needs to be sagged on the steel core. The line crew had to prepare and install the dead-end fittings already on the attack point of the conductor in the crossarm (Figure 57). The splice fitting also needs special care of installation like the dead-end fitting because of the necessity to access the steel core and clean the grease (Figure 58). All the fittings are specially designed for that sort of conductor, which increases the cost significantly. CEMIG decided to not buy the fittings from the conductor manufacturer but to design and manufacture it with the Brazilian industry.
During stringing, the tension method was adopted, and the stringing sections had to be carefully planned since the aluminum layers have a limitation of tensioning.
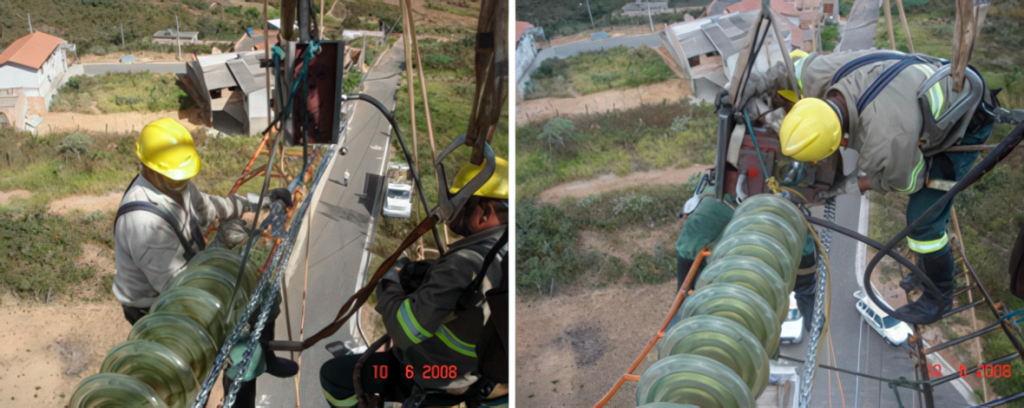
Figure 57. Details of the dead-end connection installation on the attack place
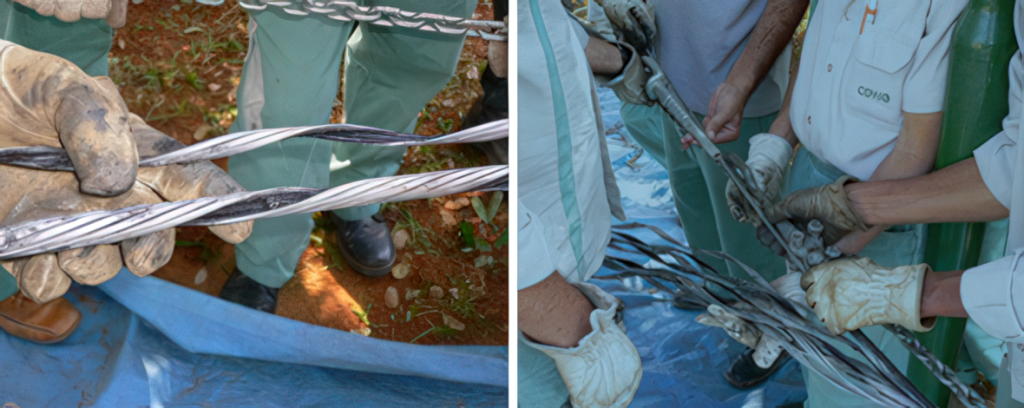
Figure 58. Details of destranding the conductor and dead-end connection handling
Conclusions
In the point of view of planning and expansion engineering, the GZTACSR conductor met the specific application, where the power line doubled its capacity. The costs of implantation of the GZTACSR exceeded 200% in comparison with a typical ACSR conductor, including consulting and training.
In the point of view of O&M aspects, additional consideration should be taken about the high-temperature grease since its life cycle is unknown by the company. The maintenance costs could be much higher in comparison with a typical ACSR conductor case.
Application of ACCC Conductor
Background
CEMIG in Brazil installed an ACCC type conductor in the uprate of the double-circuit, 138-kV power lines LD2 Barreiro 1-Nova Lima 1 and BH Bonsucesso – Sabará 1 in almost all its extension, in 2014. The original power line was able to carry 95 MVA, and its uprating would allow it to carry 220 MVA—in other words, more than the double of the original capacity of the line.
The ACCC Linnet met all premises and was the choice of installation. Table 11 shows the comparison of the characteristics.
Table 11. Comparison between ACSR Linnet and ACCC Linnet conductors
Characteristics/Properties | ACSR Linnet | ACCC Linnet |
---|---|---|
Cross-section area (mm2) | 281.14 | 245.9 |
Stranding design | 7 × 225 mm – steel core 26 × 2.89 mm (Al 1350) |
Single core |
Nominal diameter of core (mm) | 6.75 (steel) | 5.97 (hybrid carbon and glass fiber) |
Nominal weight of core (kg/km) | 217.0 | 54 |
Nominal diameter of conductor (mm) | 18.31 | 18.29 |
Nominal weight of conductor (kg/km) | 689.9 | 655 |
Rating (A) (temperature 25°C, wind speed 1 m/s, with sun) |
397 @75°C | 921 @100°C |
Rated strength (kN) | 62.9 | 72.5 |
Justification for Selection of HTLS Conductor
The choice of conductor to be installed in those lines should meet three premises:
- Meet the same dimensional characteristics of the original conductor of the line in view, to keep the original structures without changing or reinforcing its foundations
- Be capable of operating in temperatures over 100oC without impacts to the original sag
- Meet the lowest price on the market
Installation Comments
For this project, to meet the planned uprate to 220 MVA, it was necessary to add and replace 15 towers, modify insulator string configurations in three towers from suspension to floating strain, and scrap the soil in one span.
The installation had some particularities and problems. Because of the limitation of the bending radius and stringing angle of the conductor from tensioner or puller, these characteristics reflected the need of more space for the conductor assembly and installation. The tools used in the ACCC were close like those used in an OPGW installation.
The dead-end fittings and compression splices could be done on the ground but, again, because of the angle restrictions, the team decided to do it in the same way as done on the GZTACSR conductor, crimping the fitting in place, close to the crossarm. This procedure, besides the increase of risk to the safety of the workers, it also caused damages as scratches and bird caging to the annealed aluminum wires.
During the pulling of this ACCC conductor (see Figures 59 and 60), three failures occurred that were addressed to a wrong installation, according to the conductor manufacturer analysis. Because of it, CEMIG lost a big quantity of conductors. Also, because of the accidents, the construction provider refused to continue with the installation. CEMIG’s own line crew took over the project and finished the conductor installation.
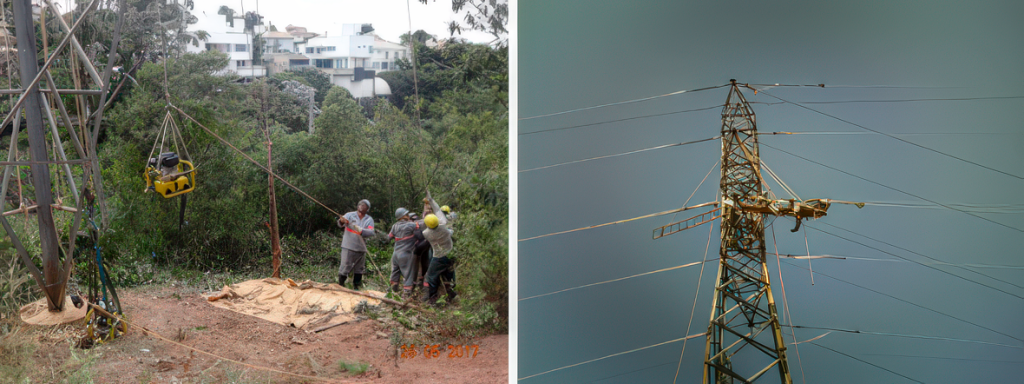
Figure 59. Details of the dead-end connection installation
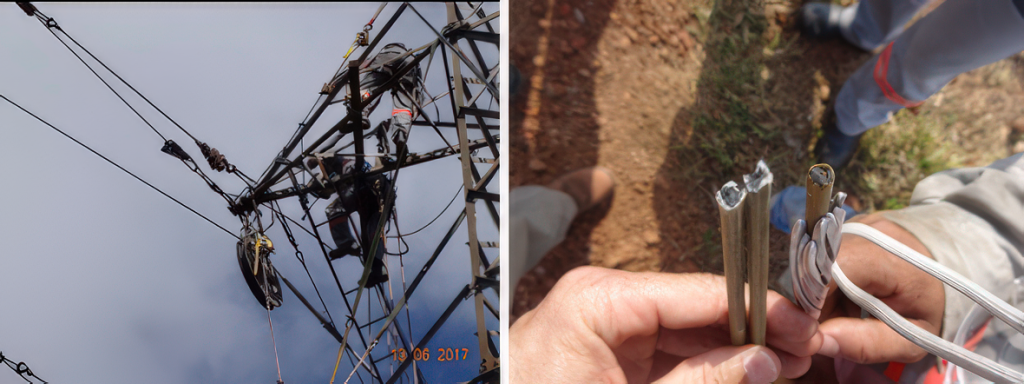
Figure 60. ACCC conductor with the dead-end fitting already compressed inside the sheave (left) and ACCC conductor damage (right)
Conclusion
The O&M analysis of this case is like the previous with the GZTACSR conductor. The particularity of the ACCC is the life cycle of the composite core, since the composite matrix of it can wear with different weather conditions, although the core is well protected by aluminum layers. The lack of information about electrical degradation of the composite core is a concern to the company.
A response of emergency restoration due to a failure of this sort of a conductor can take a longer time and be much more expensive in comparison with an ACSR conductor.
The final cost of implantation of the ACCC was a little higher in comparison with the estimate of doing the same with ACSR conductors. The costs could be a little lower on the same comparison if the failures and damages would not occur.