Background
Northern Ireland Electricity (NIE) needed to increase the capacity of a double-circuit, 110-kV line in Northern Ireland without building a new line into the area or upgrading the existing line without significant or any structural modifications.
One section of the line is located on double-circuit, 110-kV steel lattice towers (Figure 39). This double-circuit tower line splits into two separate, single-circuit portal lines (wooden H-poles at intermediates and flat formation lattice towers at angles). One side of the tower line and the single-circuit line form the circuit between Kells and Coleraine, Northern Ireland. Both had previously been strung with Lynx ACSR. As part of this overall project, the tower line section was replaced with a gap conductor and the single-circuit section replaced with an Invar conductor. Both were designed to be equivalent to the Lynx conductor (tensions, sag, size, and so on) but to have a rating of approximately 186 MVA in the summer. (The current line rating was 109 MVA.)
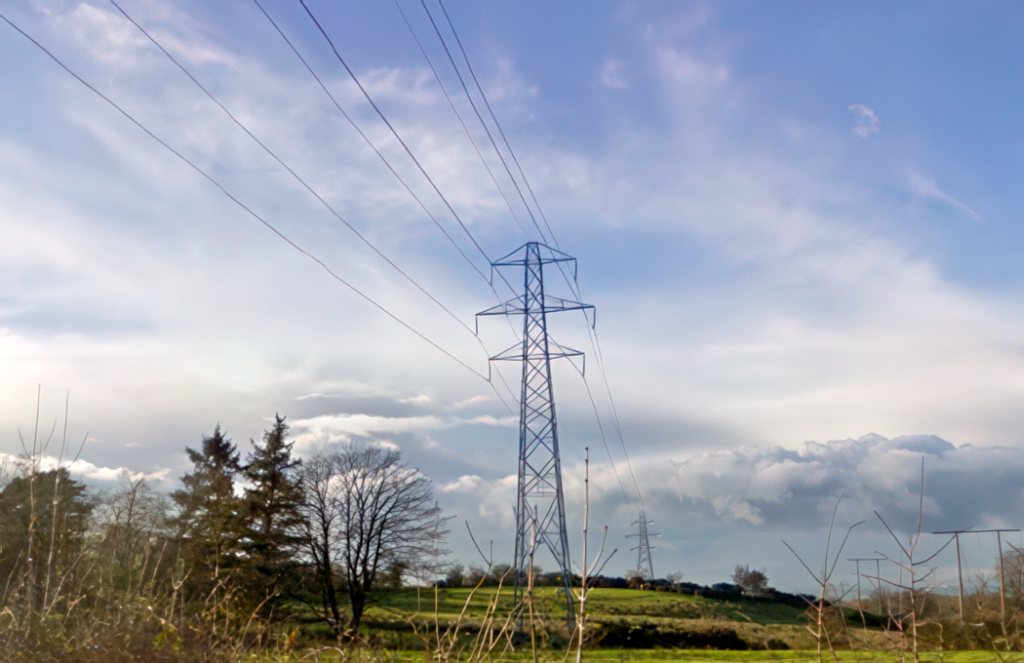
Figure 39. Double-circuit tower section
Options Evaluated
Because NIE had previously used Invar conductors on some other circuit upgrades, this conductor was considered. However, following an analysis of the conductor and circuit using PLS-CADD profiling software, it was discovered that the Invar did not perform as well with the long spans on the double-circuit towers. The sag was much greater in these spans and caused issues with ground clearance. NIE then investigated several types and sizes of gap conductors and eventually chose the 240-mm² Hawk size. The project installed approximately 13 km of gap conductor on one side of the 110-kV, double-circuit tower line.
Justification for Conductor Selection
As an existing circuit on the NIE network, the requirement was to replace the conductor and increase the capacity without modifying the structures. This meant that a Lynx equivalent advanced conductor was the best option.
Installation Review
The gap conductor was much slower to install than the conventional ACSR. NIE had to provide training sessions for its staff and contractors. There was difficulty in raising the conductor to the desired tension, and additional aluminum had to be cut back more than once. After the linesmen became more familiar with the gap conductor and had more experience in installing it, the slippage issue was better handled. The process of pulling and clamping caused some minor issues with bird caging at some locations. Overall, however, the installation was satisfactory; NIE had anticipated that additional time would be required and that some problems might arise with this being its first order and installation project.