Background
Based on forecasted load growth and planned reliability improvements, Arizona Public Service (APS) identified the need for a new 69-kV line connecting the Cactus and Altadena substations in Scottsdale, Arizona. APS worked through a line-siting process, which included many avenues of input, including meetings and comments from the local community. The identified route (Figure 34) charted construction for the new 69-kV line, approximately 3.2 mi (5.15 km) along the south side of Shea Boulevard, onto an existing double-circuit, 230-kV structure with a previously built 69-kV underbuilt line already installed. APS’s plan mandated that the existing 230-kV monopole structures would not be replaced due to the newly installed circuit—a proposal supported by the City of Scottsdale.
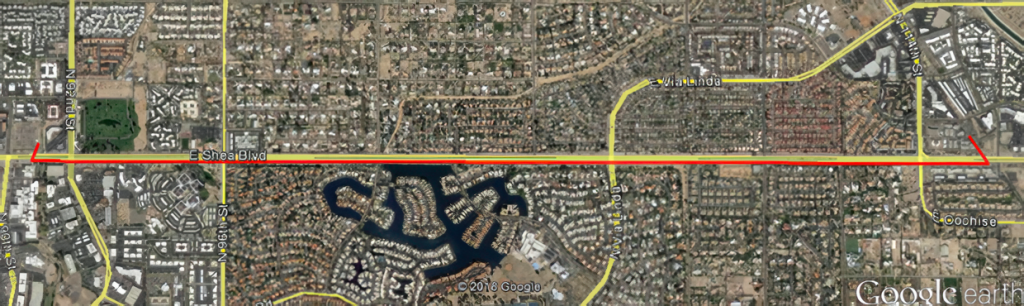
Figure 34. Map of proposed new 69-kV line
The existing overhanging 230-kV conductor was the 954 ACSR and, therefore, limited to operating below 100°C, as according to the loading limits set by APS’s transmission operations group, known as the Energy Control Center. The existing 230-kV conductor tensions were then back-calculated using industry standard light detection and ranging (LIDAR) analysis (PLS-CADD graphical sagging operations coupled with the best-known weather and conductor loading conditions at the time of the LIDAR flight) to determine the span-specific details. Because many spans are unequal, a finite element type conductor analysis was completed, and the 230-kV semi-plumb suspension insulators were also considered.
Justifications for HTLS Selection
An attempt to install the APS standard 69-kV upgrade conductor type (795 ACSS) for existing and new circuits was completed. However, due to the limited elements in the project (that is, dead-end structure capacities, 230- to 69-kV phase clearances, and 69-kV-to-ground clearances), it was clear this standard solution would not be possible. Also, because of the 230-kV circuit outage difficulties, the ability of replacing the 230-kV structures was not an option. Therefore, the next affordable option required identifying a conductor with a high-temperature tolerance and a low sag envelope.
Challenges
This alignment was located along a heavily populated section of roadway in Scottsdale, Arizona, along the south side of Shea Boulevard to the east of the Loop 101 freeway. Shea Boulevard is one of the main roadways for traffic to and from the Loop 101 freeway. As a result, work was restricted to nights only. Due to the nature of the original 230-kV structure design, a second set of 69-kV conductors was included in the original design. This resulted in the desire to minimize the loading magnitude on the structures and fit the two 69-kV circuits (new and existing) into the same space that was made available previously from the existing 69-kV single circuit. Site-specific structure modeling was completed (steel pole inspection, creating manufacturer specific structure models, and including the site-specific pole deflection) to determine the overall structure capacities.
The project also required maintaining the electrical clearances from 69 kV to non-utility structures (that is, traffic signals and streetlights) based on Occupational Safety and Health Administration (OSHA) clearances. The OSHA nonqualified electrical worker clearances were used based on the condition that these streetlights and traffic signals are not maintained by APS but instead maintained by the City of Scottsdale (or approved contractors). Based on the LIDAR data and the available reframing choices, places in which clearance issues were present required the option to build special arms. Therefore, special horizontal arms were installed using high-strength vertical post-insulators.
Options Evaluated
To find an option that created the best solution for the site-specific conditions (that is, reduced tension to manage structure loads while trying to minimize the allowable sag envelope), a range of conductor options was evaluated.
Industry Standard Conductors
The following is a list of industry standard conductors:
Industry Standard
- 795 ACSS (typical installation for an upgraded 69-kV circuit)
- 954 ACSS
3M
- ACCR_557-T16/23
- ACCR_636-T10/16
- ACCR_680-T19_v2
- ACCR_715-T13
- ACCR_795-T10/13/16
- ACCR_951-T10_v2
Southwire
- 477 Type 28 ZTACCR-TW-C7
- 520 Type 25 ZTACCR-TW-C7
- 795 26-7 ACCS-C7
- 795 26-7 ZTACCR-C7
- 795 Type 17 ZTACCR-TW-C7
- 954 Type 14 ZTACCR-TW-C7
Fourteen alternative PLS-CADD models were created for each of the conductor selections shown previously, which modified the following characteristics for each model:
- Calculating the conductor-specific MOT (IEEE-738) as according to utility-specific environmental loading conditions. This illustrated the different temperature for each conductor choice.
- Identifying the deenergized ambient initial or cold sag installed tension for each conductor choice.
- Elevating the proposed double-circuit, 69-kV attachment point(s) (because of the determined cold sag conductor clearances from the existing 230-kV conductor MOT sag) to as high as possible while maintaining the 230- to 69-kV clearances.
Incrementally, when the conductor of choice was installed in the PLS-CADD model and strung at an appropriate tension, the ground clearances could then be measured and verified for compliance. Throughout this iterative activity, the resulting conclusions were evaluated for determining the most affordable option. Figure 35 shows a PLS-CADD model.
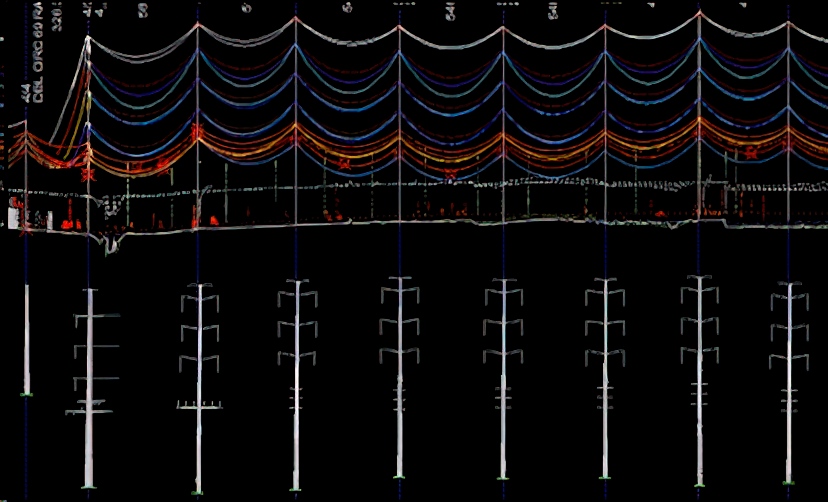
Figure 35. PLS-CADD model for the new 69-kV line
Conductor Selection
Because of the previously specified indicators and many other minor but related factors, the Southwire 795 26-7 ACCS-C7 conductor was selected. This conductor type was shown to be the best fit for the available sag envelope of minimum versus maximum conductor movements when compared against the site-specific constraints of the region (that is, 230- to 69-kV and 69-kV to ground clearances).
Installation Process
The installation process occurred at night, and the wire installation procedures were like standard ACSS installations. An appropriately sized breakover traveler was acquired with assistance from an external contractor and temporary rental of travelers. APS’s approach to the installation activity varied in its connection types from the Southwire and accessories manufacturer (PLP) recommendations. At the time, the APS construction request called for establishing an alternative dead-end and tangent conductor attachment mechanism as compared to the compression type dead-ends typically made available for standard ACSS-type installations. After working with Southwire and PLP, it was determined that the helical wrap dead-end and tangent attachments were an alternative that could be tested, approved, and supplied for installation.
Therefore, the helical wrap conductor dead-ends and tangent AGS assemblies were supplied for use on this project. Crews reported feedback related to the newer material learning curves and the significantly increased length of the helical wrap strand wires of the dead-ends (that is, 14-ft [4.3-m] long).
Conclusion
The overall HTLS conductor options are a costlier option when measuring the material costs as compared with traditional ACSS-type conductor installations. However, in many cases, the additional costs related to replacing structures may outweigh the increased cost of the HTLS conductor.