Background
As part of the plan to deactivate the Michoud generating facility, Entergy New Orleans, LLC, determined that two leads from the Ninemile generation facility needed upgrading. The Ninemile to Napoleon 230-kV line feeding the warehouse and central business district of New Orleans and the Ninemile to Derbigny 230-kV line serving the New Orleans Superdome1 and adjacent area of the city required increased capacity. These two lines are entirely enveloped in the urban confines of New Orleans plus a crossing of the Mississippi River and four Interstate 10 crossings (Figure 12). The lines were constructed in the late 1960s on steel poles, except the river crossing, with average spans of 300 ft (90 m). With the urban landscape, closeness to streets, homes, shops, and congestion, replacing the structures was not an option; the existing sag profile for MOT had to be maintained. The project was a good candidate for an HTLS conductor.
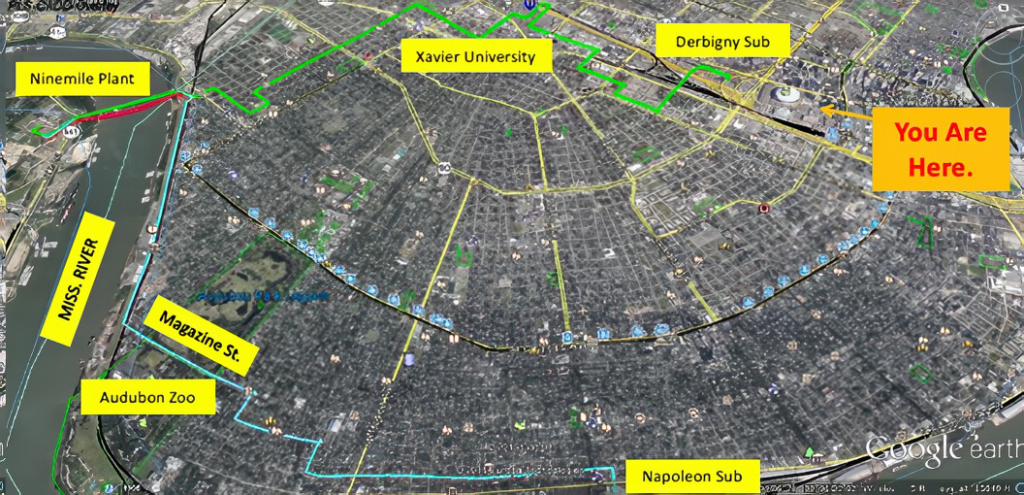
Figure 12. Project overview—New Orleans urban area
Conductor Selection
Entergy’s upgrade included converting the steel pole davit arm framing to a braced post (Figure 13). This conversion eliminated concerns about vertical load from a larger conductor on the existing davit arms. The braced-post framing easily transfers the vertical load component up the brace to the pole shaft. Entergy also uses mostly guyed steel poles for angles, which makes tension increases for larger conductors more manageable as well. The increased loads can be transferred to the guys and anchor poles rather than being supported on self-supporting poles.
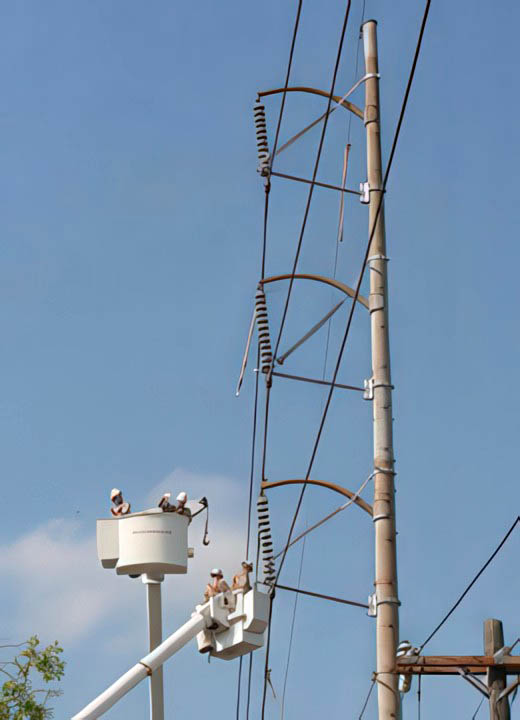
Figure 13. Conversion from davit arm to braced-post framing
The original conductor on these lines was already a larger diameter and capacity (1607 amps) conductor, and the upgrade in capacity to 2100 amps required ample aluminum cross section even at elevated temperatures to maintain sag limitations. A full gamut of HTLS conductors was evaluated, and the ACCR Diver with a MOT of 200°C (392°F) was selected as a solution. The HTLS provided desirable sag performance compared to the existing conductor and eliminated the need to replace structures (Figure 14).
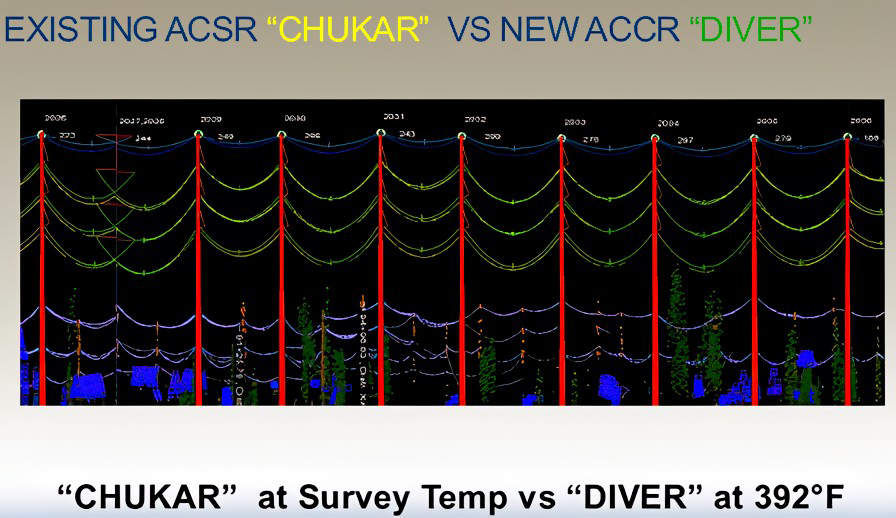
Figure 14. Sag curve comparison
Construction Phase
The construction plan was built around three stages, as follows:
- Stage 1: Pre-pull—reframe davit arms to braced post, put wire in blocks, 2–4 hours per pole
- Stage 2: Pull—set up for 29 pulling segments, 48 mi (77.25 km) of the conductor
- Stage 3: Post-pull—remove stringing blocks, clip in wire, two to four hours per pole
Many of the poles on both circuits had distribution under build and multiple distribution crossings. Many of these instances were worked with the distribution circuits energized and rubbered for protection.
Because the full length of the lines involved in this project were urban, work was done in very close proximity to homes, businesses, and landmarks (Figure 15 and Figure 16). A lot of work was invested in public awareness of the construction schedule and progress so that the public was cognizant of the road and street closures that were required to perform work. Outreach programs included meetings, websites, and news media bulletins of work activities to mitigate the impact on the work areas and the public.
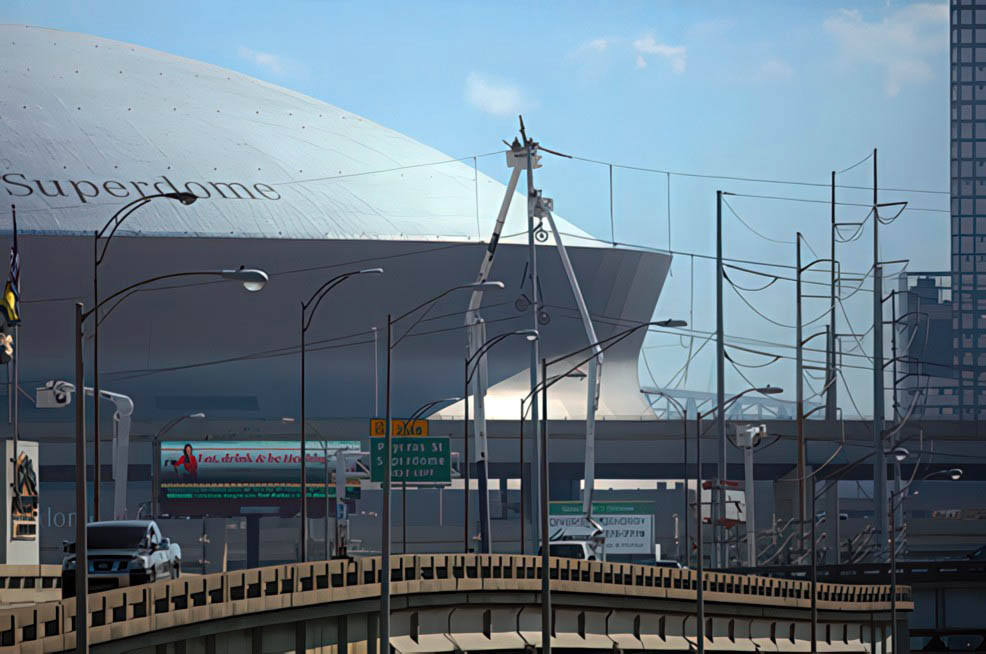
Figure 15. Stringing wire near the Superdome
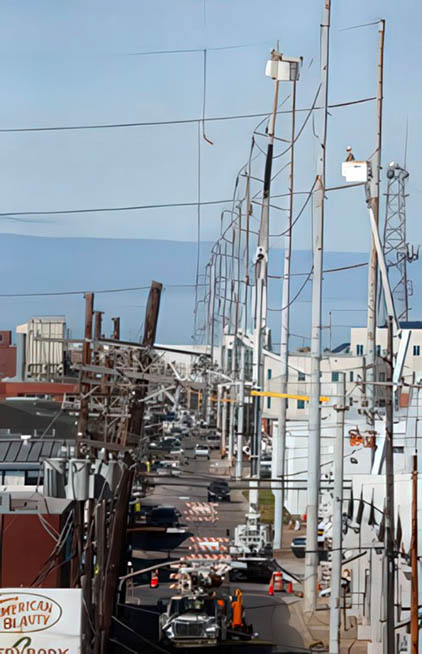
Figure 16. Urban construction congestion
1 Superdome is a trademark of Totes, Inc.